Like any other area, bodywork production in Győr meets state-of-the-art standards, with more than 2,000 machines running in a busy shift. The welding clamps are electrically powered, allowing faster, more accurate, more reliable and quieter operations and easier handling than the previous pneumatic solution. The comprehensive machine park is made up of gripping, positioning, clinching and flanging equipment, as well as welding workstations for special tasks.
The TT bodies are built on a floor area of 85,000 square meters. On both sides of the main lines, groups of robots weld together individual components such as underbody element assemblies, wheel arches and side-sills. The body, gradually upgraded with a bulkhead, a back plate, pillars, side panels and a roof, is finally fitted with the bonnet, tailgates and side doors. It takes 3.7 hours to produce a single body, including 2 hours for building it and 1.7 hours for delivery.
Production is currently carried out by a small team of just under 50 people per shift due to low customer demand. Colleagues build the two TT models, the Coupé and the Roadster, according to the build sequence, in phases, moving from equipment to equipment, following a program schedule. So when entering the hall, one hardly sees any colleagues working, only in isolated areas. Nevertheless, it is impressive to see so many robots waiting for the car bodies ready to start performing automatic operations.
Superstructure, chassis – lines 1, 2, 3, 4
Our guide, Attila Schler, gives us a brief foretaste of what is in store: “Here the front sidewalls, frame setting, over there the clinching and riveting take place, and it is there where the roof is fitted,” he points to the right. “Then the suspended elements are installed in the Audi TTs. The different lines are called body shell and underbody (superstructure and chassis) 1, 2, 3, 4, etc.”
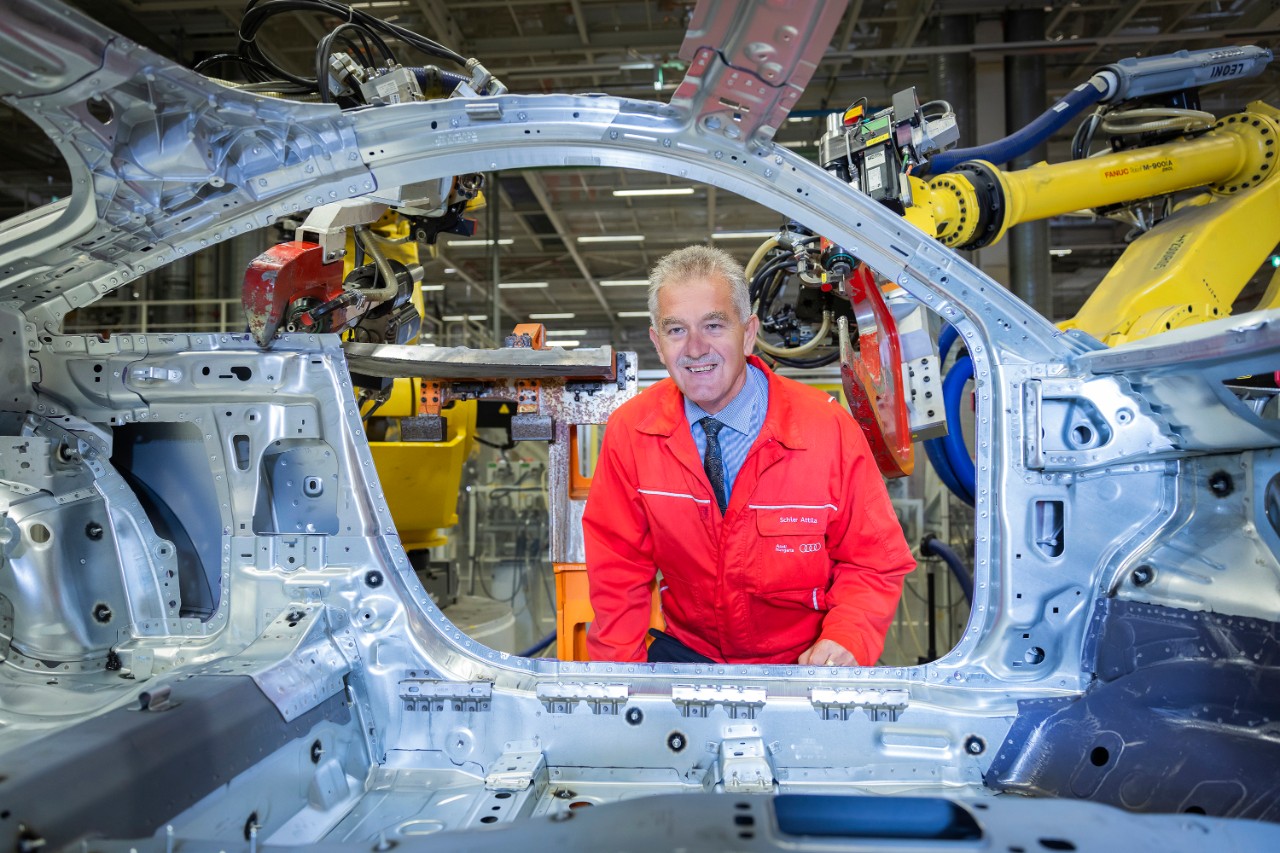
The body shell & hang-on-parts are made of aluminum. Most of its components come from the press shop we visited earlier in this series, but there are some parts that are not from Győr. The underbody is made of steel, much of which is hot‑formed high-strength steel, but very little aluminum is also included.
Due to time constraints, we are not following the build sequence of the car, as our goal is to give an insight into the birth of the TT, which offers a first-class, unrivalled driving experience.
Upon arrival at the chassis area, we are passing by the finishing underbody line, line 4, where 100 percent dimensional control, visual inspection and arc welding are done by our workers, and together with some automatic equipment, they all guarantee the excellent Audi quality. We are now passing by the manual workstation where the footplate is preassembled for the Roadster. Our guide in line 3 explains that this is the area where the floor level chassis receives its bulkhead and wheel wells. Line 3 includes a TT-specific supplementary line, line 3.A, where aluminum elements are already fitted to the chassis. That is because the TT chassis is integrated into the underbody line of the A3 Limousine and A3 Cabriolet (built in Győr between 2013 and 2019).
In the meantime, I have received the notes of our guide, which contains a non-exhaustive list of the types of bonds found on the TT. Brace yourselves, here come some serious technical details: 128 FDSs (flow drill screws), 3,033 spot welds, 1.9 meters of core welds, 1,149 self-piercing rivets, 78.8 meters of strength bonding, 5.1 meters of laser welding, 44 solid rivets, 207 clinch rivets, 1.8 meters of rabbeting and 6 SBs. Bonding technologies on the superstructure include 112 clinch rivets, 1,149 self‑piercing rivets, 35.3 meters of gluing, 22.5 meters of rabbeting. So there is still a lot to learn if we want to manufacture a car, especially a TT, where only the chassis is made up of over a thousand parts. And what about the Roadster? Sixteen different assembly technologies are used in the production of the Audi TT Roadster body, ranging from resistance spot welding on 2,963 work points to 77.16 meters of high-strength bonding. Wherever possible, welding and bonding are carried out in one operation, saving time, cost and weight. At the end of each line, a separate measuring device checks the dimensions, and maintenance also constantly monitors and reduces energy consumption, whether it is electricity or compressed air, through various improvements.
Wedding of rear-, front floor & front longitudinals
In the blink of an eye, we are already in chassis line 1, where the front floor plate, the side-sills and the rear floor plate are welded and from on the car goes to welding and gets its chassis number.
The production schedule comes from Ingolstadt, is fed into the plant management system and that is what production is based on. The rear floor plate is the lead, followed by all other parts. Everything that is specific to the vehicle is made here in the press shop. When the underbody is ready, it is transferred to the other side via an overhead conveyor system, arriving at the beginning of Aufbau 1. Columns A, B and C form the inner sidewall—they are built into the cars along the assembly lines in a fifo (first in, first out) sequence, explains Attila.

In the body shell hall, we meet a colleague who, we learn, is in the process of manufacturing rainwater troughs and lamp seats. He puts the parts on a geometric fixture, clinches them together, or depending on the technology required, the machine performs the operation. Automation in the body shop is 70 percent for TT production. There are only a few manual workstations, such as the one for the production of roof support parts.
Nowadays, at the end of a production run, the number of units produced is low, explains our guide. In the past, 40-50 bodies were produced per shift, 60-70 at peak times, but now only 17-18 cars are assembled per shift. This requires a financially sustainable workforce. There is a small team that first assemble the smaller units, then move from department to department. For example, they first make the sidewalls and the accessories, and by then, the chassis also arrives from the other part of the hall.
Weddings also take place in the body shop, which is where we are now: the chassis gets the inner sidewall in Aufbau 1. The Roadster is different from the Coupé: it has the roll bar in the front windscreen frame, which comes from Ingolstadt together with the rear passenger protection unit, we learn.
The next line is where the outer sidewall is built in, and the so-called “frame adjuster” frame fits it into position. It gets fixed and then the robots come and rivet it to the chassis and the inner sidewall. This is followed by a 100 percent geometric check to guarantee a perfect fit of the doors, fenders and bonnet.
The roof is welded on with a laser technic. On both sides, two robots weld the roof to the sidewalls. The perfectly precise position of the roof—depth, position from front to back and side to side—is ensured by a device called the “roof bell, Glocke”. Its operation is very fast and efficient, but the settings need to be adjusted very carefully. For example, the roof should fit almost seamlessly against the sidewalls. Imagine the two welded seams being welded in parallel by the two robots in about 25 seconds. Quite an achievement!
At the end of the line are the finished bodies: you can see which parts are made of high-strength steel and which of aluminum. Of course, the work is far from over here. Now comes the rigorous inspection. The strength of the welded bonds is verified by ultrasonic inspection during chassis construction, and on the finished bodywork, specially trained colleagues check the bonds and the surfaces and finishuing defect free surfaces before painting a car. But we now have a car shape, and the TT’s muscular tail and perfectly smooth features are clearly visible, although the stern-looking matrix LED headlights are a long way from getting installed in it. Our journey continues. We are grateful to Attila Schler for guiding us around and sharing with us his expertise. We are off to the paint shop, which we will cover in the next part of our series.