Harmony. That's what we feel when everything is in place. It’s just a good feeling, a sense of calm that overcomes us when we sit down to interview Robi. Our development engineer, still only 32 years old, came to Győr from Debrecen, on the other side of the country, as an intern in 2015. He graduated from the University of Miskolc with a degree in energy engineering, where a semester-long course in noise and vibration protection caught his interest and he decided to pursue this field.
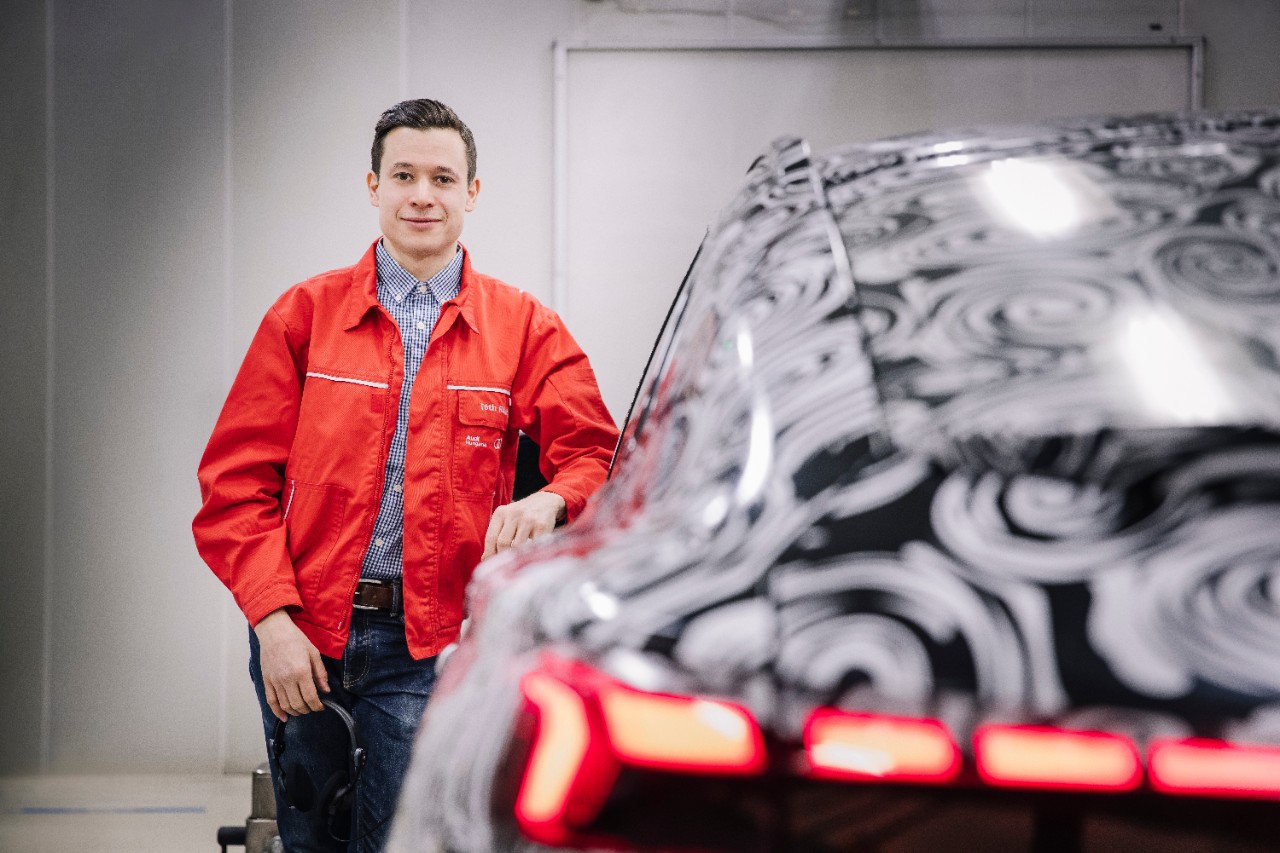
"I wanted to come to Győr because of the development work at the company, where I wanted to be actually involved in the life cycles and development of a product, which was my dream as a student. As an intern, I was immediately involved in acoustic activities, where, to praise the company's HR, they found the right measurement tasks for me. The theoretical knowledge gained at university was quickly reinforced by the product-specific technical knowledge gained during the internship. Here, we are looking at the acoustic properties of the drives, from a mechanical point of view, using non-destructive external tools, so that our measurements help us get an overview on various components – oil pumps, bearings, etc. From the customer's point of view, we also measure the sound effects on the driving experience. Our job is to ensure that the product, the drive that we manufacture here in Győr, goes into series production in a way that is acoustically perfect."
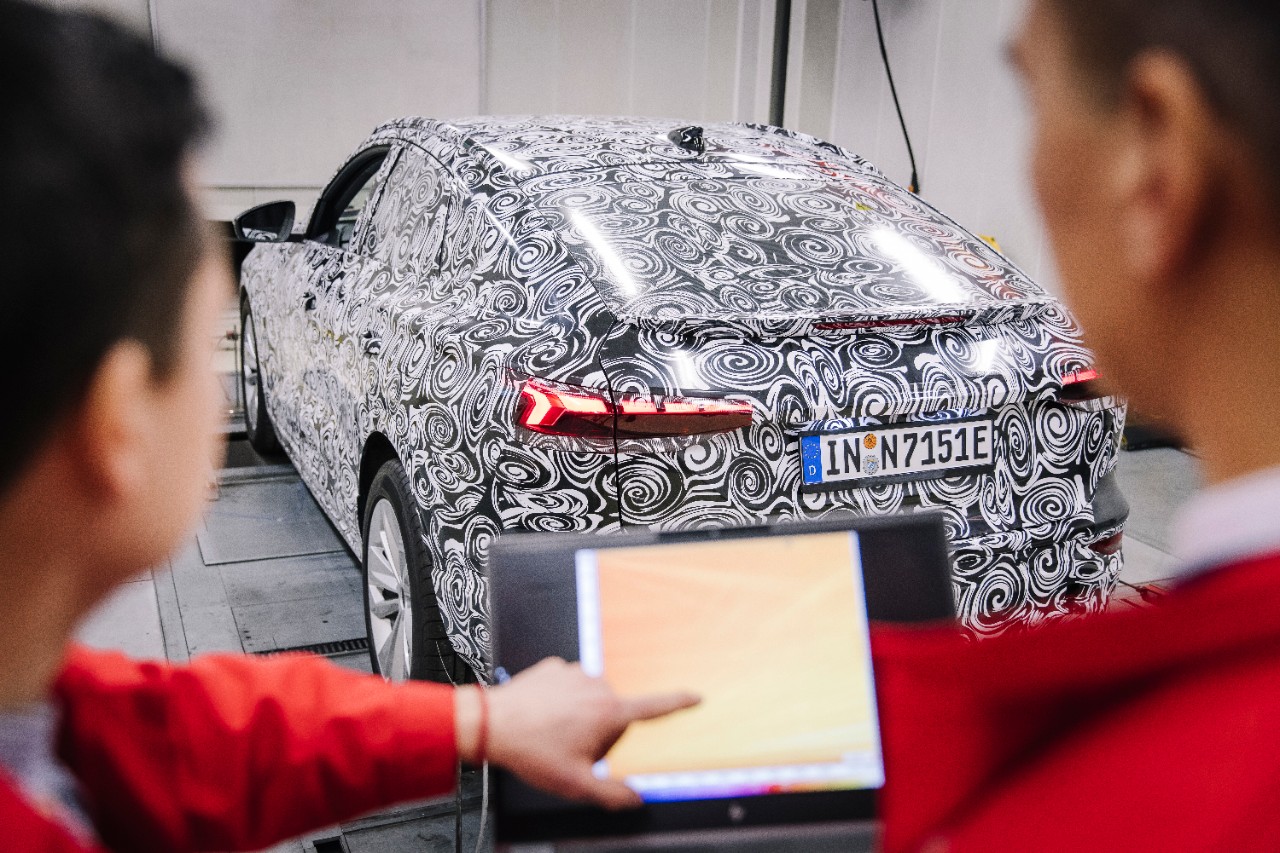
How have the products you have tested changed during your years with the company?
"It's not only my scope of activity that has changed, but also the portfolio under review. I have mainly worked with small internal combustion engines, most notably the EA211 in-line four-cylinder petrol engine, but I have had the opportunity to test all the company's powertrains. Each product has its own specificity, but drawing on our acoustic knowledge we always have our solid points of reference, and we can help each other within the team."
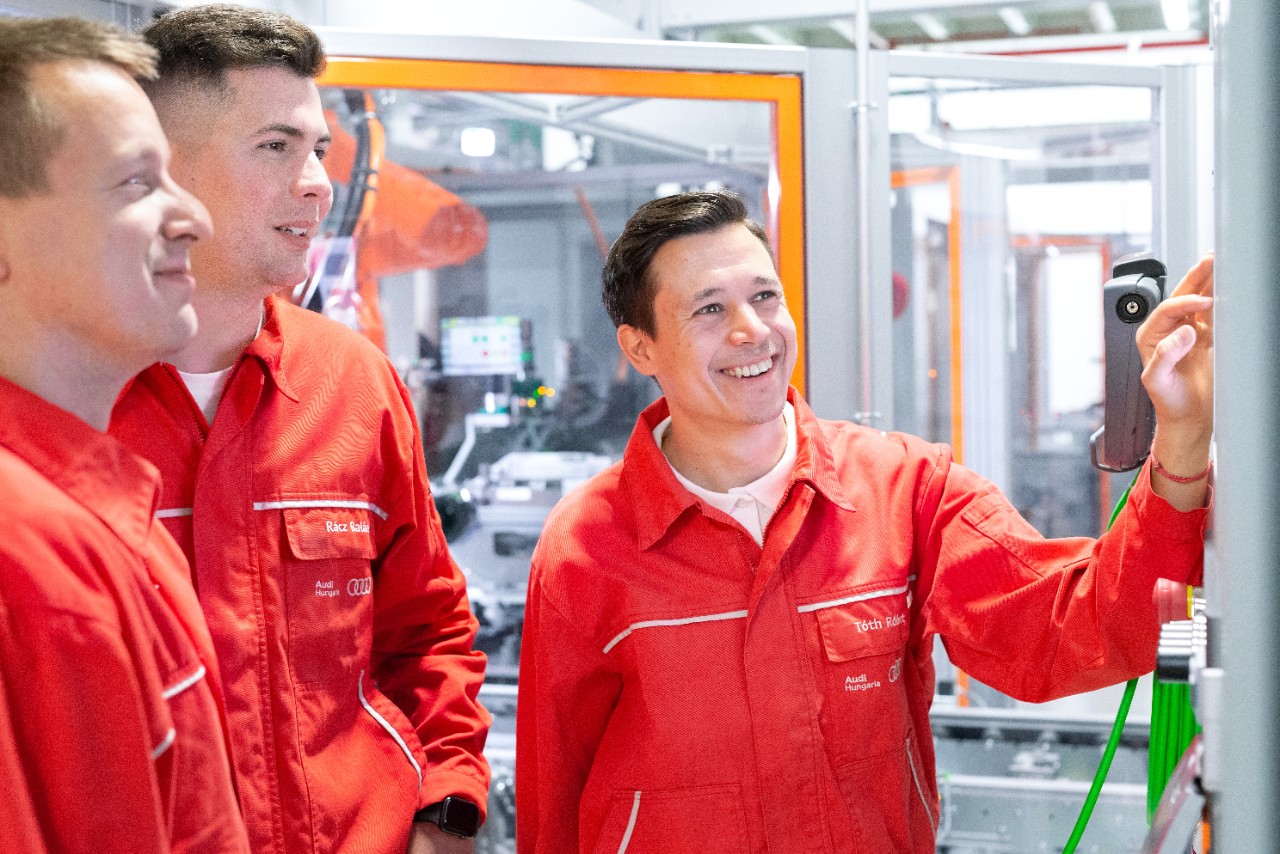
Each member of the acoustic development team is responsible for a drive derivative, so their job a great source of pride but also a great responsibility.
"At the factory level, in addition to the development team, there is also an acoustic team in the MAC, the Experimental Engine Manufacturing Center, who work on testing pre-series products, and in production, acoustic colleagues work with the assembly line results, with whom we are all in contact. Our team is responsible for client liaison and helps with series integration."
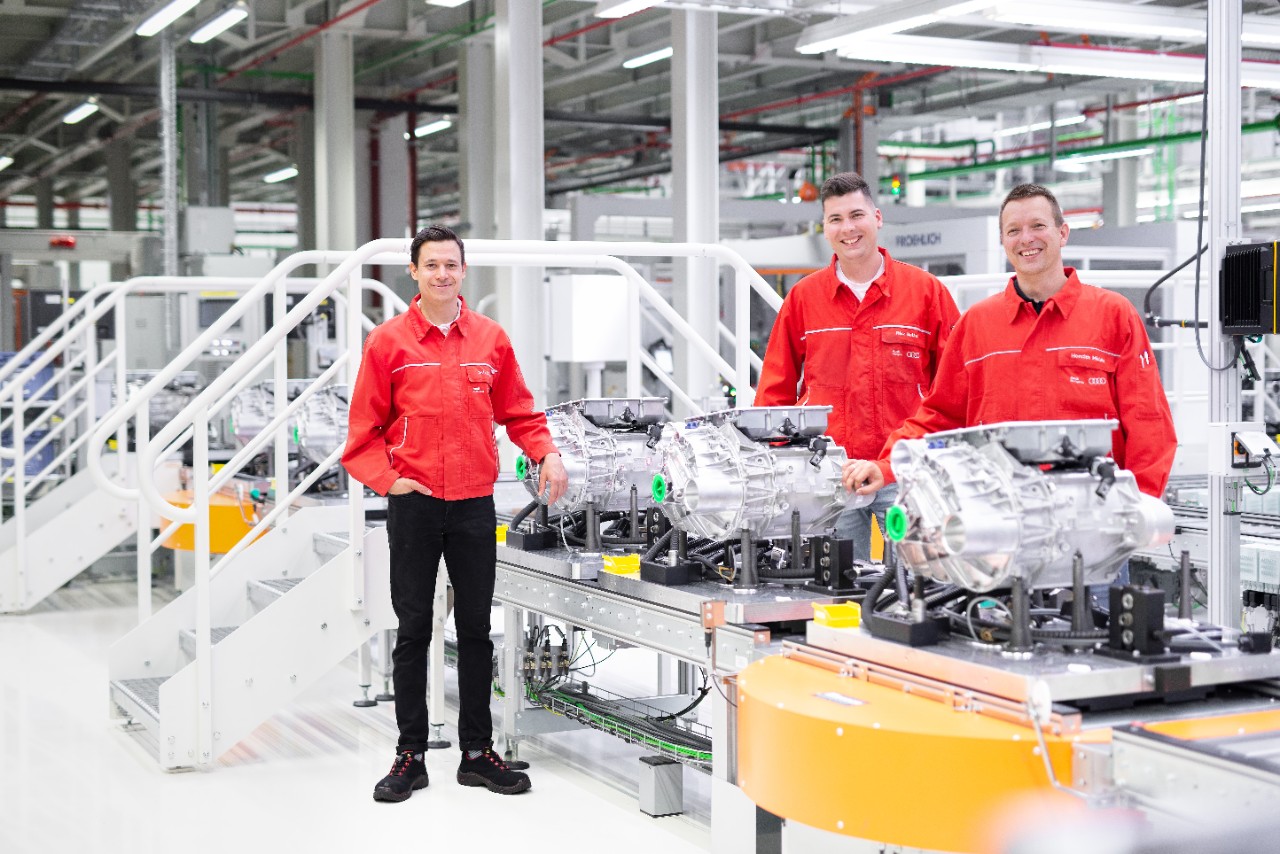
After the internal combustion engine, what kind of new situation did the arrival of electric drives bring about?
"CBEV was a great challenge both professionally and in terms of work organisation. The technological leap also brought with it the need to improve my knowledge, and acoustically this period brought a lot of new things. It was during these years that the close link between production and development was established, as the new product type required more intensive and faster communication among the areas of technical development, MAC, quality assurance, production planning and manufacturing."
The next stage of development for Róbert started with a posting to Ingolstadt, where he spent a year in Germany to learn about PPE electric drives.
"It was a fantastic time, I learned a lot, and I came back to Győr with a completely different professional approach. I learned what I needed to learn, and I am grateful to my mentor. Here in Győr, we now also manufacture the gears for the PPE drives, which is great and a real success story. As a coordinator, I brought together the different acoustic areas related to PPE, such as simulation, mechanical design, manufacturing, measurement. I understood the process from component state to the built drive and integration into the vehicle. I can only echo the closer cooperation that started with the production of the CBEV, with excellent communication and joint work between the two areas. Our acoustic team was involved in the development of the PPE drive at a fairly early stage, which has brought many benefits to the process. Each drive, including the PPE, has its own vibration pattern, which can be used to infer the acoustic characteristics of the individual components. Among other things, we determined the limit values and laid down the measurement standards together with Ingolstadt, after learning about the characteristics of gears, bearings, etc. We've tested the drive in future models on the run test stands and on the factory floor, and we're now monitoring production after it has gone into series production."

What makes your work special?
"For me, it's being able to do what I've always wanted to do. It’s varied, interesting and comprehensive. It's varied because I’m surrounded by lots of different people, from different areas and international locations. It's interesting, because there are always new challenges, and it's a constant source of renewal. It's comprehensive because we don't just see the product itself, but we can take a holistic approach, we can follow its whole life cycle."
Interesting facts:
How has the field of acoustics developed? Initially, their activities were approached from a quality assurance perspective, from a customer feedback perspective. But now acoustic development is integrated early on in the development process.
Do you need good hearing? Not specifically, but it can be improved. When listening to classical music, you can distinguish the instruments, and by listening to them you can develop your listening skills and concentration. Noise can be visualised during the tests using the software.
Development and production hand in hand: This is a great advantage for our factory in Győr, as it allows us to work more closely together, we have a better overview of each other's processes. We know each other personally, and the daily contact also facilitates communication.
What makes it high-tech? To determine the exact location of acoustic excitations, an acoustic camera is used.