The Audi TT goes through the same paintwork process as the other models made in Győr. Let’s take a closer look. The raw bodywork arrives, the birth of which was described in our previous interview with Attila Schler. The bodywork is pre-treated and degreased. It then goes through a cathodic dip painting (Kathodische Tauchlackierung or KTL in German) – remember this because we’ll come back to it later. KTL is an electrostatic process in which the bodywork is the negatively charged cathode and the liquid itself acts as the positively charged anode. The bodywork is then dried, followed by a sealing stage (called PVC), where the sealant is applied by robots. There are manual processes as well, with several seams. Once this is complete, the bodywork gets a filler coating or filler primer. Four colours (black, grey, red and white) are used to fill any unevenness on the surface (approx. 40 microns thick). Next, the bodywork is dried again, before it is sent to a sanding shop, and then a base coat is applied (the colour of which depends on the customer’s choice of the car’s colour). This is followed by an intermediate drying step, and then the colourless topcoat is applied, which actually provides surface protection and gives the body a glossy finish. “The process mentioned above takes place in hall G60, but we also work in building G61, where we produce custom-coloured bodywork parts (e.g. bumpers, mirrors). We also need to talk about the HRK, or cavity protection, where wax flooding is applied in hall G80, that is, the assembly line. Roughly 400 litres of flooding wax is injected into the bodywork, which will only hold 1 kilogram, or between 0.9 and 1.0 kilogram for the TT,” describes Dávid Rómeó Ganczler in a nutshell of what we are about to see.
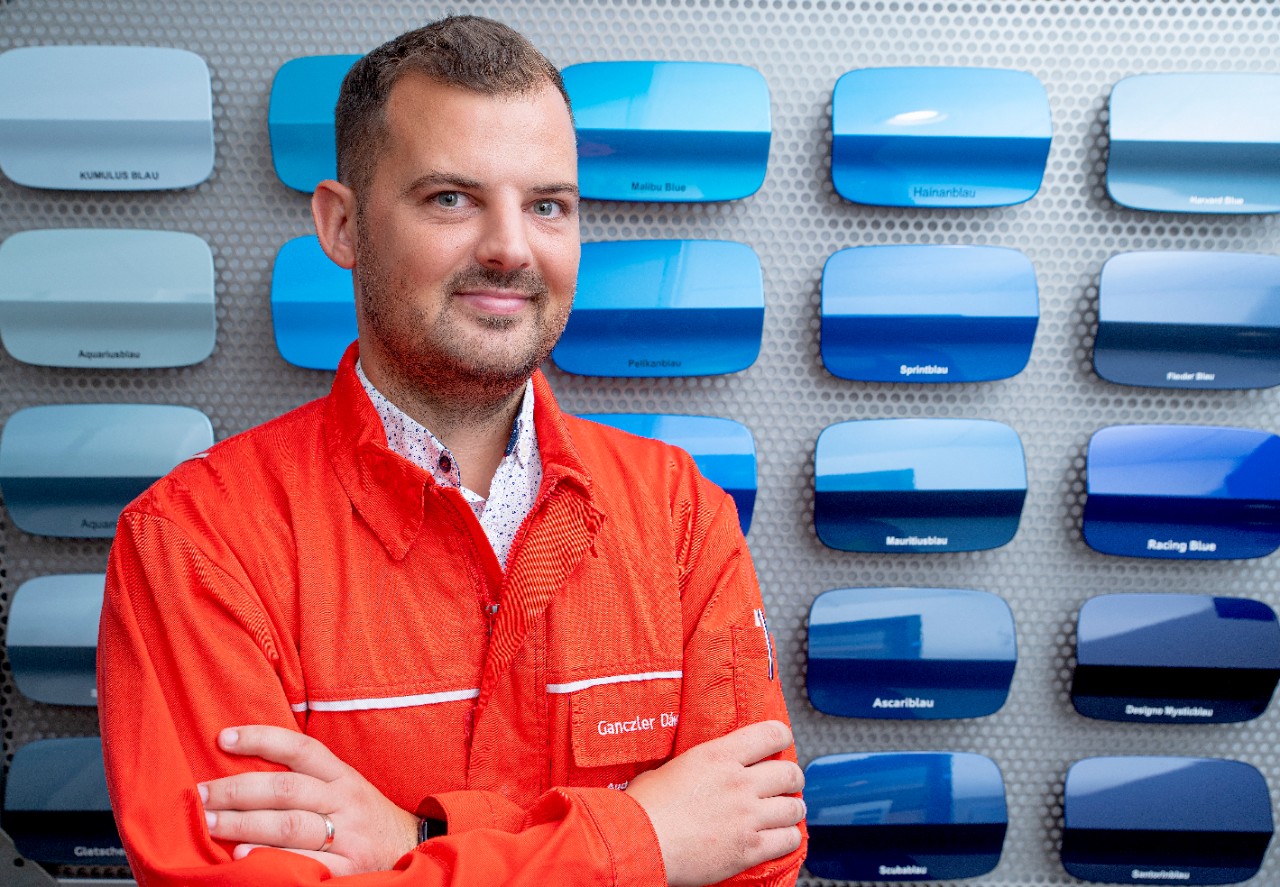
Put on the overalls
The exciting journey starts with us getting dressed, as special overalls are the required workwear at the paint shop. We also put on our fashionable outfit and set off to explore the paint shop.
You would be surprised to learn that the paint finish, that certain metallic shine that all Hungarians once longed for, is much more than just a thin coat of paint. 13 kilos of sealants (identified by the abbreviations GAD, FAD, UBS and SDM) are applied to the car in the form of various seams. On a raw bodywork it means about 23 kilograms of paint and sealant materials in total. Yet the thickness of the paint coatings is roughly that of a human hair.
In the paint shop, work takes place on two main levels – at zero metres and at nine metres. The air temperature is lower on the ground floor, because the dryers are located upstairs, and significantly heat up their surroundings, meaning that you will not feel cold around them.
During the preparation process, small tubs are used in 12 zones for removing the sanding dust, grease and any dirt from the bodywork, similarly to the cleaning applied in a car wash. Next, a phosphate layer is applied, which provides corrosion protection for surface damage, and then comes the aforementioned KTL coating. This is also a dipping bath in a huge tub of 440 cubic metres, full of constantly refreshed liquid. It is not recommended to take a dip in it, even though my mind wanders off to a cool beach during the plant visit.
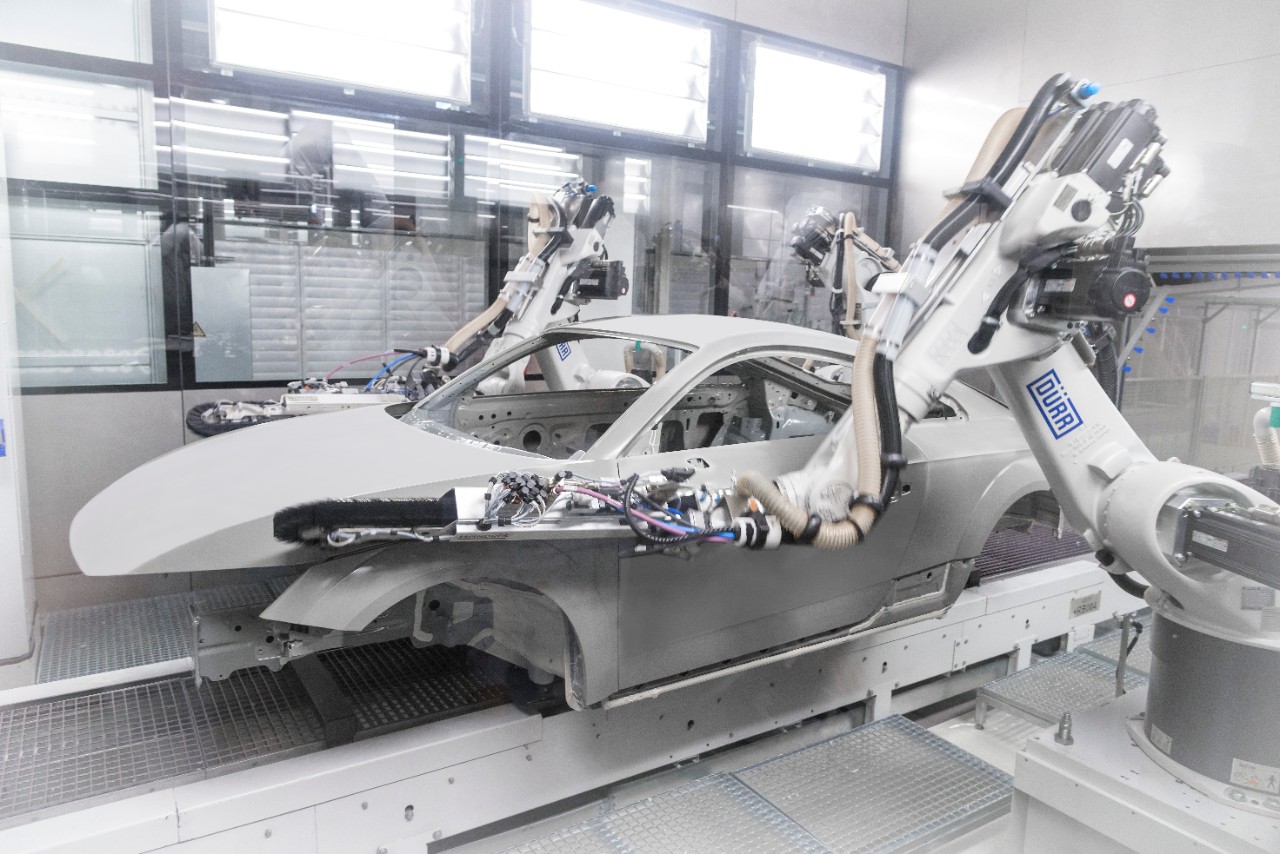
Rómeó tells us that nearly 500 employees work in the paint shop, currently in three shifts, from Monday to Friday. The shop also operates a number of machines, robots and equipment, so maintenance personnel and equipment operators are always on duty to ensure smooth operation.
TT in the bath
Although we can’t see it all, we are shown proof that the bodywork makes a full turn in the KTL tub. The current and temperature values are continuously controlled. During the drying process, the applied hard coating is cross-bonded for added corrosion protection, such as to protect the body from seemingly innocent stone chippings that will later cause rusting. This protection is further enhanced with UBS seams.
In the first few minutes, we don't see any TT’s in the paint shop. Rómeó Ganczler says that we don't have much chance to catch a glimpse of one. And just then, there’s one right in front of us, taking a dip in the bath. The dip paint makes a big puff, as a sort of greeting, when the car submerges in full. The bodywork should only be left in the KTL bath for a certain period of time – 8 to 10 minutes, no more and no less. According to the engineer – and we’d better believe him, as he’s an engineer –, the KTL would cover 90-100 square metres of surface, should the bodywork be laid out. Less top coating is needed, since there is no need for covering the bodywork completely, but only where it is visible.
After the bath, the bodywork is transferred to the dripping and cleaning zones (five in total), and then on to the 180 °C dryer. It spends 40 minutes there, during which time it heats up to around 140 degrees. As I said, nobody gets cold in this area.
The entire painting process takes eight hours. Which is exactly the duration of one shift. Most of the time is spent with the drying. The preparation and KTL only take an hour and a half in total.
After the paint has cured, the fasteners and spacers that the bodywork received before the KTL process are removed, the Bemiks (spacers) used for the subsequent painting processes are transferred, and the sealing plugs are fitted, which will be melted into place during the subsequent drying. Steel and aluminium have different finishes, with different shades of ochre. In the paint shop, some work is done by hand, as the removal of glue contamination or eventual surface defects mainly requires manual sanding; however, sometimes machine sanding is also used. The surface is dusted and, if necessary, repainted.
Takt time seaming
In the meantime, we notice a change in the line, with the bodyworks transferred from the ground carriers (SKID) to the hangers (Gehänge). In the next process, the employees insert rubber plugs in the bodywork, which is important for its protection, and prepare the bodywork for PVC sealing. A liquid sealant, of which there are three types according to thickness and use, is applied by three robots in the first cell. A total of 24 robots work on the PVC line, three of which used for opening the doors. The seams are applied with dowels of different sizes to takt time.
In another cell, four robots check by using a flash of light that everything is in the right position. They know where and when to move based on the programmed figures. At a next stage, a broad seam is applied (UBS), which is, however, much thinner than the previous one. It is intended only as a protective layer and not a sealant, and is mainly used in wheel arches and the chassis. Also, it is not spread out, but sprayed. However, even the robot is unable to take care of everything. At the UBS spreading takt, human workers use brushes to cover positions where the robot cannot reach.
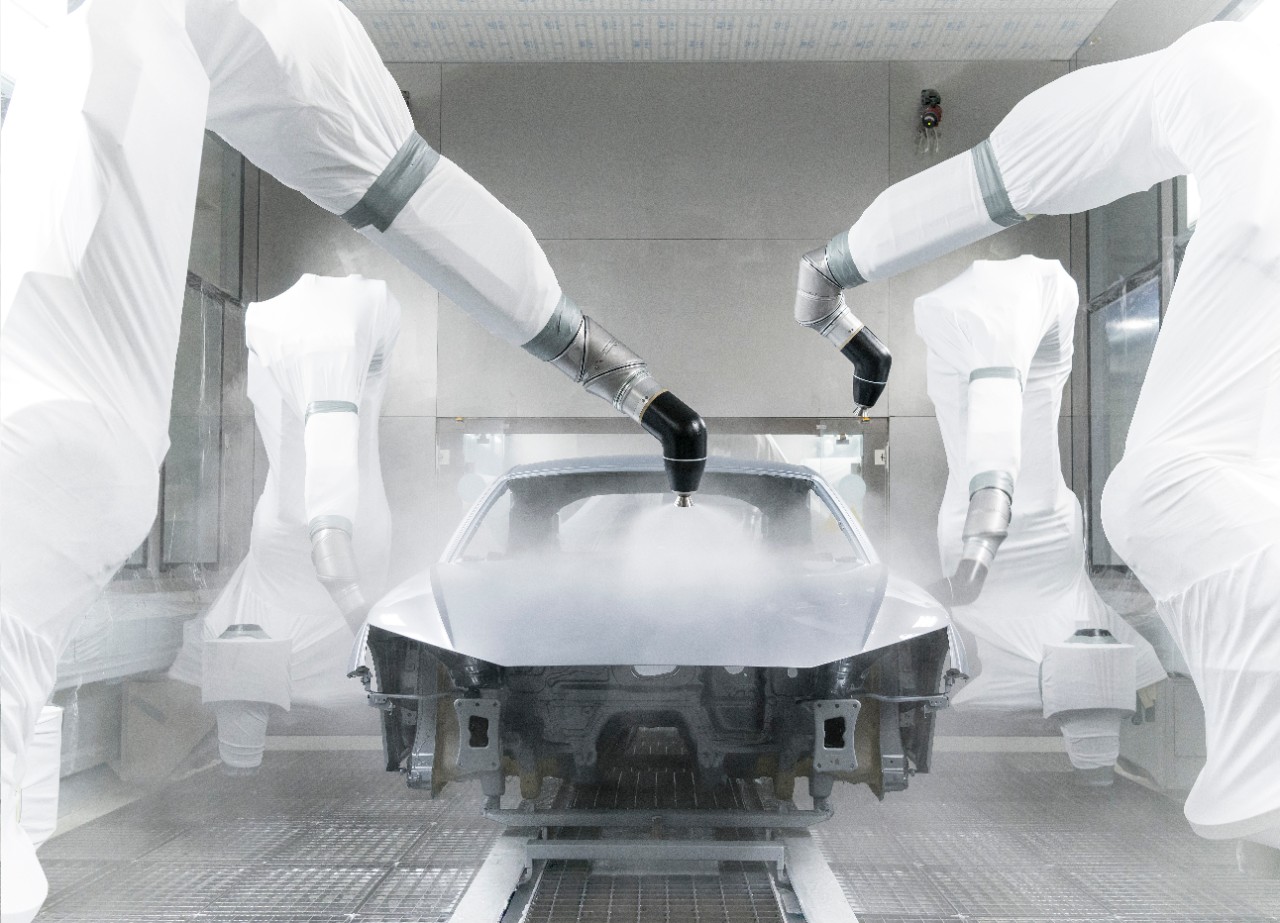
We arrive at the moving walkway, where the staff remove the excess sealant and ensure an aesthetic finish. “The TT is a critical model for us, translating to a higher workload for colleagues, because it requires more meticulous work. On average, work is 30 seconds longer. If they had to work with TTs all the time, that would be a problem. There are so many tiny edges, so many things to touch up,” says Rómeó with a laughter.
Next, the sprayable damping material (SDM) is applied. If you have seen the inside of a bodywork, it appears in the form of grey seams. With an important role in acoustic, noise and vibration damping, 2.5 kilos of material are applied on the bodywork, the interior parts and the bottom of the dashboard. I haven’t mentioned it yet, but each station has quality control. If anything has to be fixed, there is a separate workstation for that.
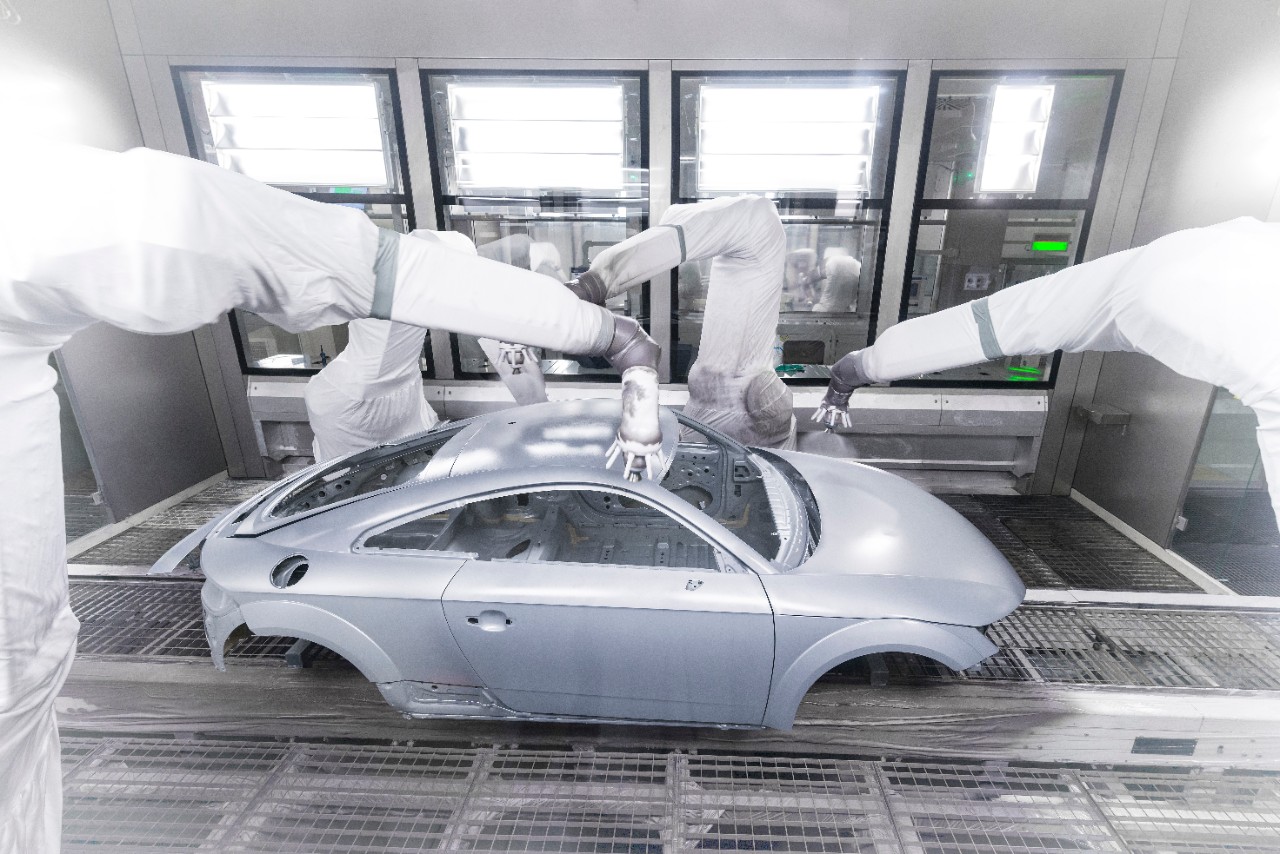
At the end of the sealing line, the bodywork is lifted from zero metres back to nine metres, where an ionisation gantry dusts the body, and then a robot at another station wipes it clean with a sword brush. Next, the Audi TT then arrives at the filler area, where the robots spray it with a 35-microns thick coating, followed by a 15-micron base coating, and finally a 40-micron colourless topcoat. After the filler coating is applied, the polished bodywork is seemingly finished. However, this is far from being true. It is already dusted, and the primer has been applied. As mentioned earlier, one of four different colours of base coating is used. This unit has 14 robots, 8 of which open doors. The sealing paint is applied on the inner parts first, and then on the outer parts. A total of two kilograms of primer is applied on a single bodywork. Once this is done, the TT is dried again at 150 to 180 degrees, and then sanded, dusted and colour coated. After being transferred for intermediate drying, it is only dried enough to allow the colourless topcoat to adhere. This process ends with the finish, where we are right now. Here, the final stage consists of sanding and polishing. Interestingly, while the grinding wheel in KTL has a coarseness of P400, the one in the Füller phase is rated P6-800, and the one at the finish is rated P3000-P5000.
Finished, polished bodyworks arrive on two final receiving lines. The light is refracted in the two light tunnels so that expert eyes can spot even the tiniest of defects. If a defect is found, the bodywork is transferred for rework, where the workers polish and sand the surface to perfection. I can’t take my eyes off one of the colleagues, who is devotedly stroking an Audi TT coupe painted Python Gelb. The intimate moment is soon over. The yellow cyclone, which I wish I owned, is about to enter the assembly line. Before it is grabbed by the protagonists of the fourth phase, it receives cavity protection at the HRK stage mentioned earlier.
“We rarely see so many TTs in a single day. I think they have lined up specially for you,” adds Rómeó as he says goodbye to us at the door of his office. We take off our overalls, which I ask to keep – they will serve me well when I paint my flat later.