There is not one single employee who does not come into contact with it – as I have learned – there is not a single work cycle (takt) in the car factory during which the Audi TT or Audi TT Roadster arriving on the production line does not require some attention – at least for a stroke or a caress. But let’s not rush ahead. Let’s start from the very beginning.
The Audi factory in Győr is huge – after all, it is the world’s largest powertrain factory. All the engines for the Audi TT are also built on this site, even back in the days when not every stage of the assembly process was done in-house. Since 2013, however, almost every part of the TT has been made in Győr – of course, there are quite a few parts that we source from suppliers, but there are some from Győr and Győr-Moson-Sopron County, even among them as well. Powertrain production, production planning, development, quality control and testing are not covered on this occasion. We’re just following the main production flow. We’re going to visit four factory areas – the press shop, the body shop, the paint shop and the vehicle assembly shop – and we are going to present our impressions and the information we learned in four articles. Stay tuned: it’s going to be exciting!
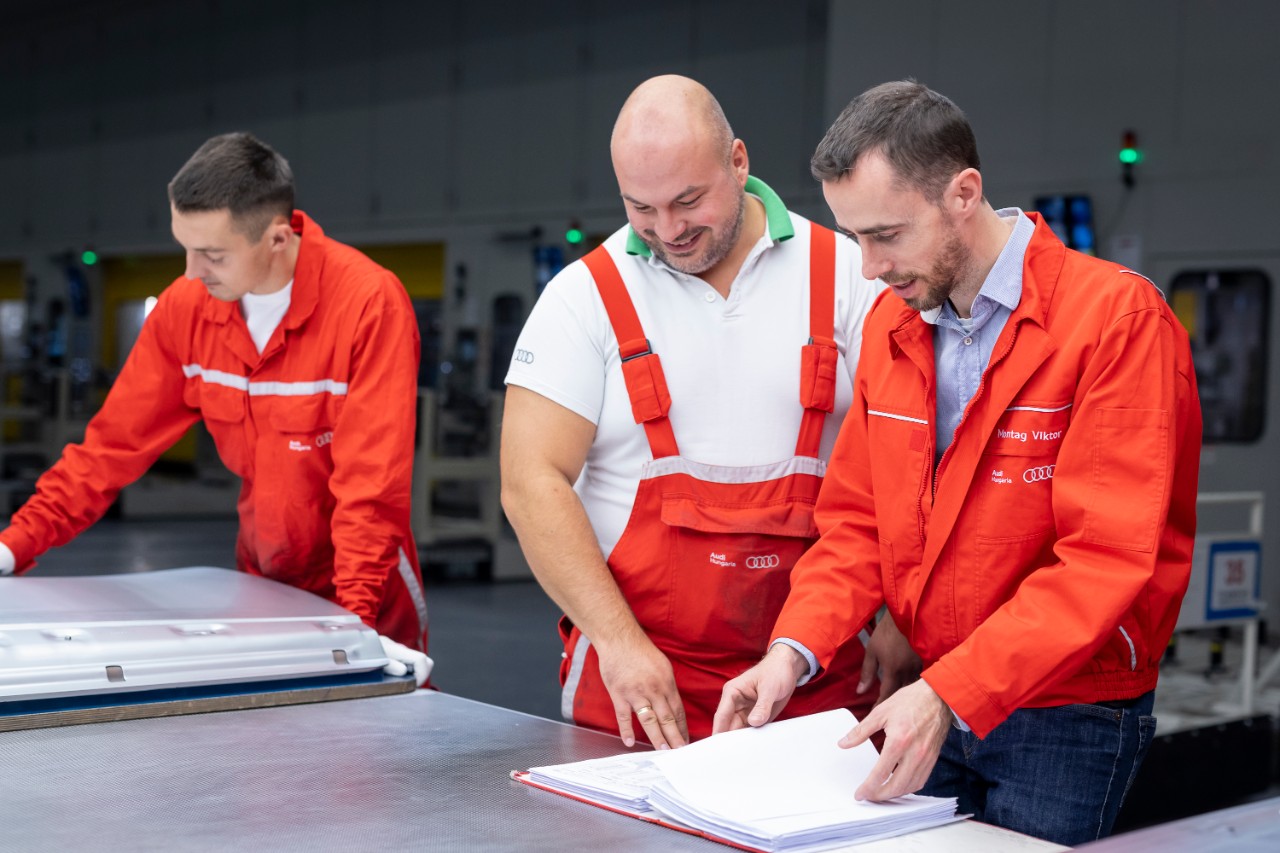
Press shop, where metal plate becomes a component
The aluminum coils, weighing 5-9 tons, and steel coils, weighing up to 33 tons, arrive by rail at an off-site warehouse in Dorog, from where they are transported to the factory on special flatbed trucks, says Viktor Montag, Senior Production Planner at the press shop, sharing the first steps of the production process. The aluminum coils are then lifted off by crane to an intermediate workstation, where they are cut and then continue their journey in three directions. Some of them are shipped to Bratislava, where they are processed on a press similar to the one in Győr, while the rest land in the tool factory and, of course, at the Győr press shop, where the Audi TT sports cars come to life. The pressed-out parts are stored in a finished goods warehouse, and the body shop picks the right part according to its own needs. “In the case of the TT, we process mostly aluminum, roughly 80 percent aluminum. Everything on the outside of the car is made of aluminum. Everything that is steel is mostly on the inside, including the floor plates, the wheel arches and certain structural elements,” explains Viktor Montag.
The press shop is noisy, especially when you get close to the two Schuler machines: the cutting machine has clocked up 70 million strokes and the press roughly 25 million strokes in their lifetime, since they were installed in 2013. Prior to that, lacquered bodywork came from Ingolstadt, then for the first and later second generation TT models. For the third generation, which debuted in 2014, the body panels were already being made in the Győr press shop.
The focus in the press shop is on balancing: getting the right quality products and minimizing the offcuts. The incoming material volume is around 40 thousand tons, of which about half will be technological waste in the first round. This is of course reused under the company’s Aluminum Closed Loop scheme, which involves the closed-loop circulation of aluminum, allowing the valuable raw material to be reintroduced to the cycle with the same quality.
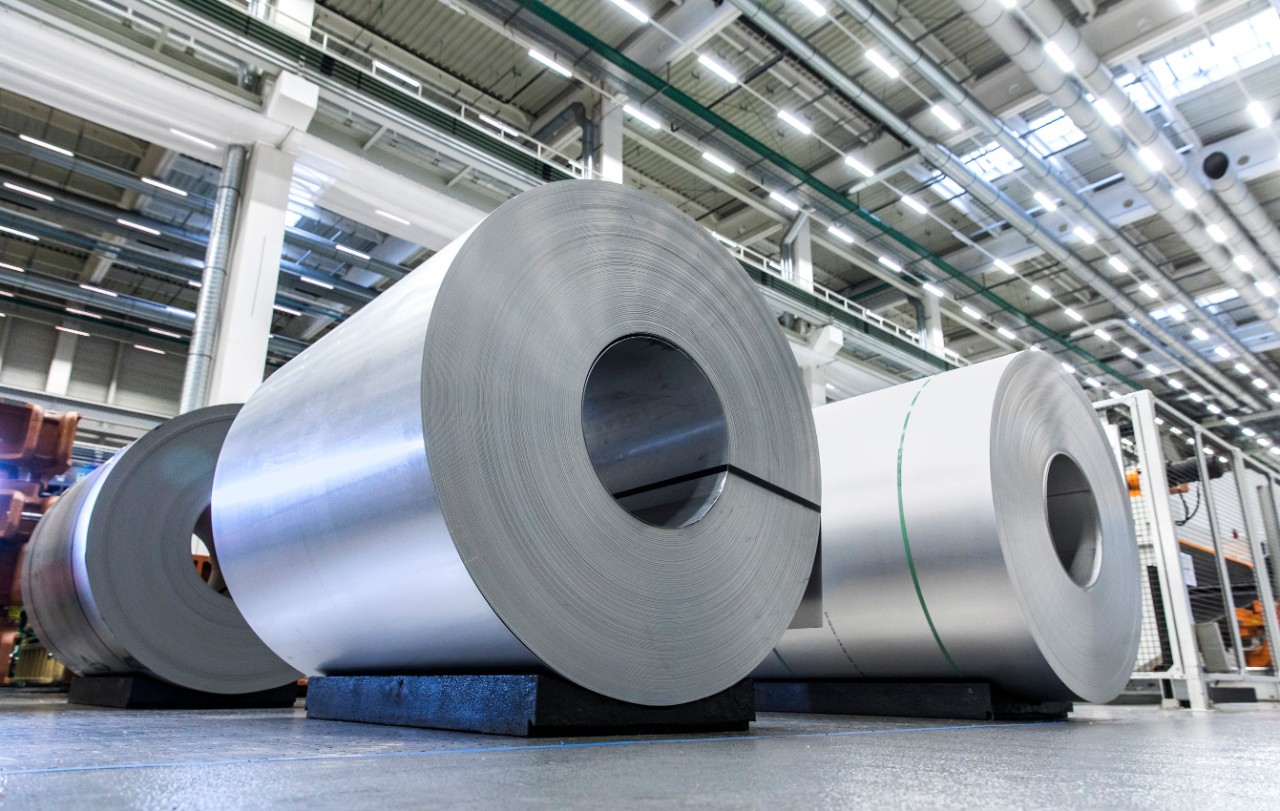
In the press shop, where around 180 people work, wheel arches and sidewalls for the TT are being made and preparatory work is being carried out with 8-ton forklifts alongside a large crane. We are passing by the sheet pit, where the continuous movement of the coils, interrupted, slowed down and smoothed in contrast, ensures the undisturbed flow of the steel or aluminum plates. With 106 TT press tools (deep drawing, cutting and punching per part, up to several parts being produced per punch) in the Győr plant, there is a tool for every application. Some of the tools are made in the neighboring tool factory. There are plenty of these and, after the TT’s farewell at the end of November, a good number of them will be recycled, but some tools will continue to be manufactured. In the process, TT parts will be pressed for years to come for the repair shops. Of course, not in such large numbers...
Tons above us, tons around us
We are arriving at the press, which has a total weight of 81,000 kilonewtons, or 8,100 tons. The parts transfer is robotized, but there are also people working in the pre-assembly area, lifting the tools with cranes. Above us, tools worth hundreds of thousands of euros and weighing 15-20-40 tons are pulling away, controlled by an employee with a remote control similar to a game console.
Positioning the plates in the press is a spectacular operation: a pair of robots prepare the plate so that it arrives at the deep drawing station in the precise position. They observe characteristic points, typically corner points. Meanwhile, Viktor Montag also gives us some figures: the head press, where the molding takes place, weighs 2,100 tons, and the follower presses weigh 1,200 tons each.
Moving on to the end of the process, let’s take a look at some parts. But not alone; 7-8 workers alongside the two conveyors (since most parts are made in pairs) carry out a quick visual inspection; single-digit seconds are all they need to spot any fault. Another colleague also inspects the parts more thoroughly in one-hour cycles (every hour or every 400 pieces) using a whetstone to peel their surface to see any surface defects, count holes, and check other quality criteria. Quality control is therefore also – so to speak – continuous during the production of the TT. There is also a quality control independent of the press shop workers: one automotive part per production run is taken out and thoroughly inspected. This is now done by quality assurance here on site at the press shop. If there is a fault, the faulty products must be found immediately, and the cause of the fault identified and corrected.
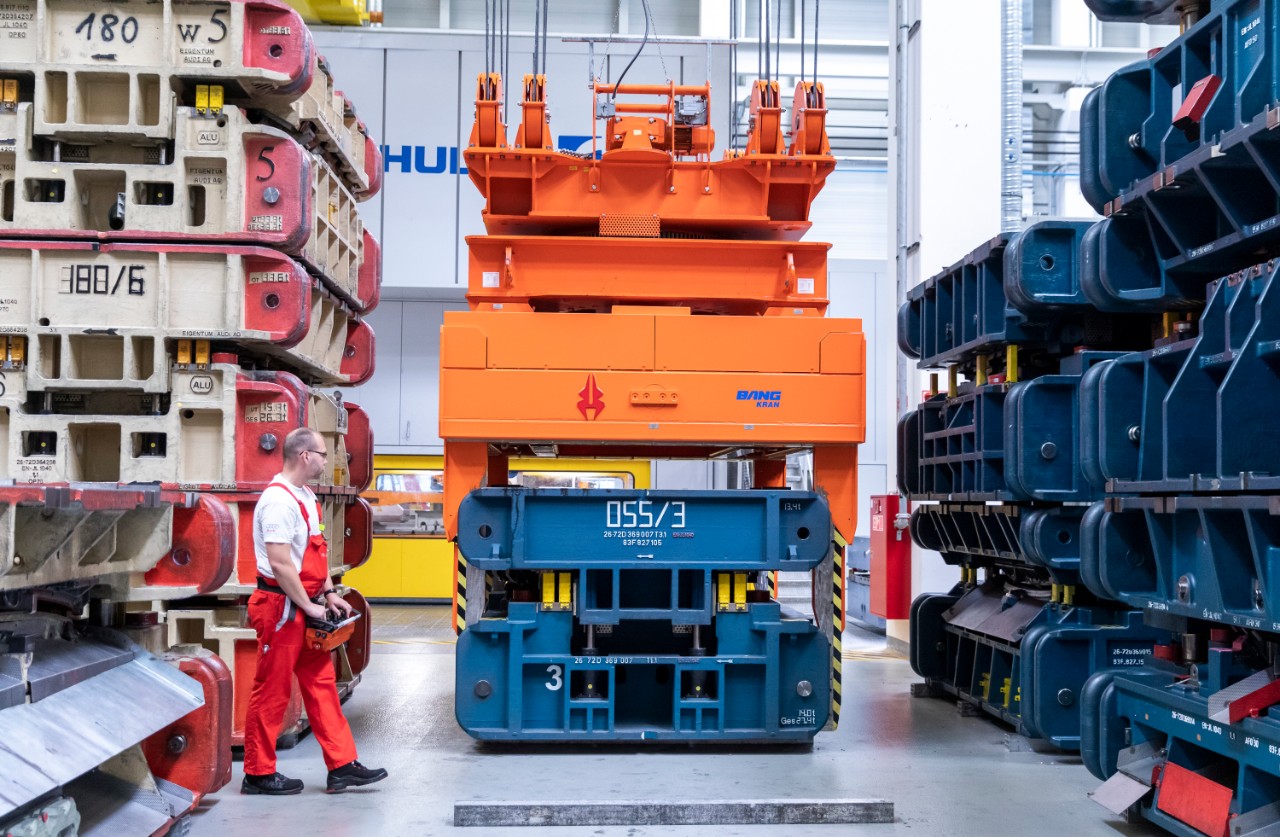
Featherlight parts
We are continuing our journey between finished products and samples: those are the exterior and interior of steel wheel arches, and this one is a floor plate. “There is a bit of unevenness on the steel, which is not a problem with this part, but with the aluminum fender, which is visible, the finish has to be perfect,” explains Viktor in confidence. “The part is light as a feather; I can lift it with one finger. The Roadster’s front windscreen frame is also light, but making it isn’t easy. The main difficulty is that a lot of windscreen frames come out of one coil, and aluminum becomes increasingly difficult to process over time. A coil can last for more than a year and needs to be tested separately for its further usability. For comparison, for a sidewall, we cut off one coil at a time, and the plates or pressed elements are used up in a few weeks. So how to work it out it causes a big headache,” says Viktor. Solution: buy more Roadsters, folks... but that is me adding at the exit of the press shop, where we can hear again – the presses are indeed quite loud.
Small batches and aluminum – these are TT characteristics. We also learn that the material takes 2-3 months in the coil form, a day in the coil buffer, an hour on the cutting machine, and a few days as a sheet, to leave the press as a component after five minutes. At the end of the process, some familiar shapes can be seen. How is the sidewall made? “On the cutting machine, we cut out the expansion holes and the corners, essentially getting a very wide contour, followed by the deep drawing, where we don’t cut anything. Then, after the major part of the mold is finished, we cut and reshape it in sections, sharpen the radius of the prominent edges, prepare the tank opening, and the wheel wells, and then make further small cuts, shaping, drilling and punching holes. You can’t condense it all into one operation; you have to separate it, at least in our company. It is design versus tool construction costs,” explains Viktor.
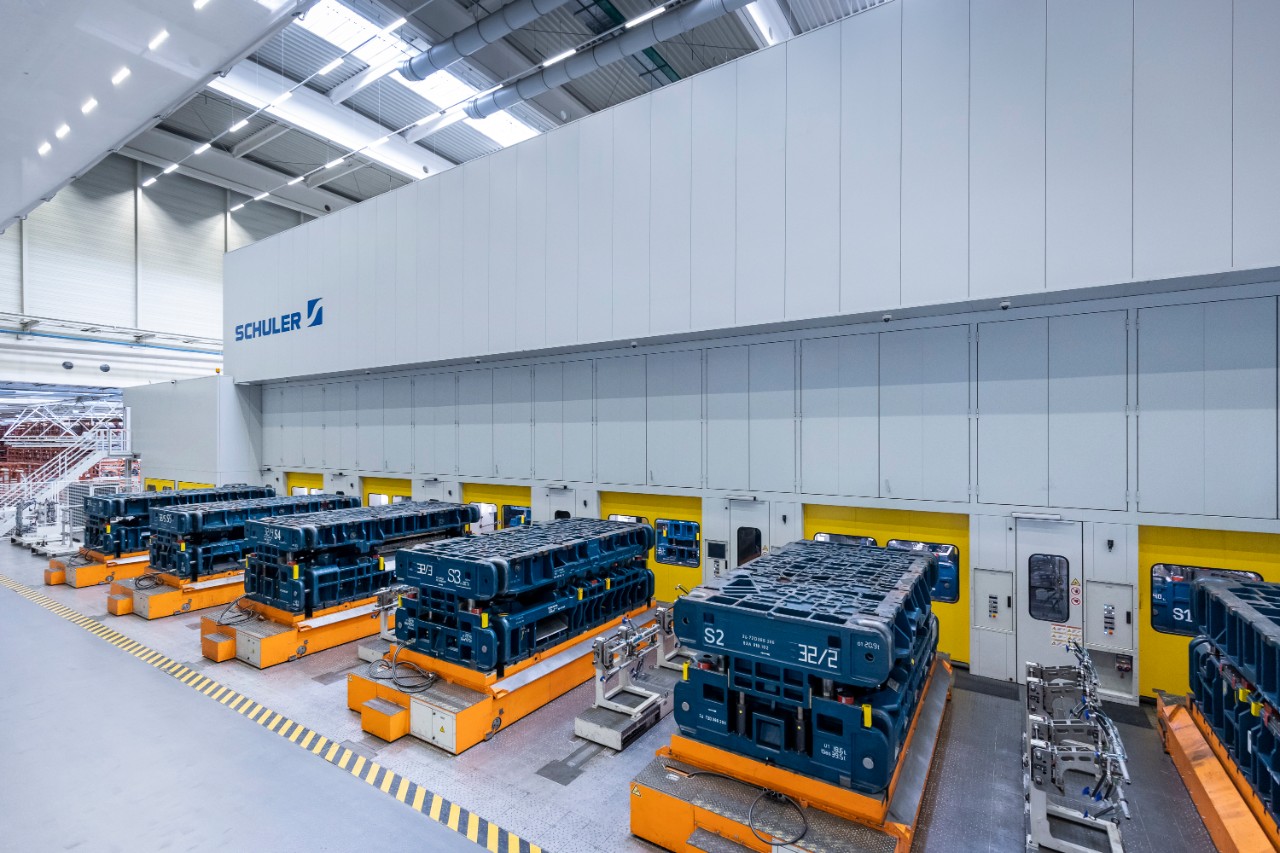
But of course, the TT cannot be seen only rationally, in terms of numbers; emotions also play a significant role here. Like all Audi Hungaria employees, Viktor is very sorry to say goodbye to this legendary model. “Although the TT presents us with some production difficulties, we love it, because it is ours and its third generation is made in Győr to the core. We’re proud to produce every last part of it,” concludes Viktor.
In the next part of our series, we’re going to visit the body shop.