Human-robot collaboration at the Tool Factory
We can find some particularly fresh innovations in the company’s Tool Factory, where we make bodywork parts for the exclusive models of the Volkswagen Group. The production of doors, mud guards, bonnets, boot doors and side panels takes place in flexible robot cells. With so many configuration options, it’s no wonder there is a growingdemand for digital solutions and automation technology. With this in mind, in the summer of 2022, our colleagues in the Equipment and Appliance Manufacturing department put a new, innovative technology into operation: a collaborative robotic gluing station developed by our toolmakers in partnership with the collaborative robot experts at AUDI AG. The great thing about the new technology is that human-robot collaboration is no longer constrained by space. Unlike with industrial robots, here there is no need for a protective perimeter – the human is able to work safely alongside the robot. During the work process, one of our colleagues prepares the parts before pressing the start button to initiate the gluing process, which is then carried out by the robot. With the new workforce operating in shifts, everyone wins, as processes become more stable. In addition, by optimising the parts preparation process, our colleagues have also saved around four kilometres of travel per shift.
This is not the first time that experts in this area have used their decades of experience in automated robotic cell construction, however. In December 2020, a robot designed specifically for the Engine Factory was put into operation to performtasks related to the production of four-cylinder Otto engines. The robot lifts engine blocks weighing almost 30 kilograms from a multi-storey raw material pallet onto the production line, while also lifting and sorting the separating elements individually, significantly reducing the occupational safety and ergonomic risks for our colleagues.
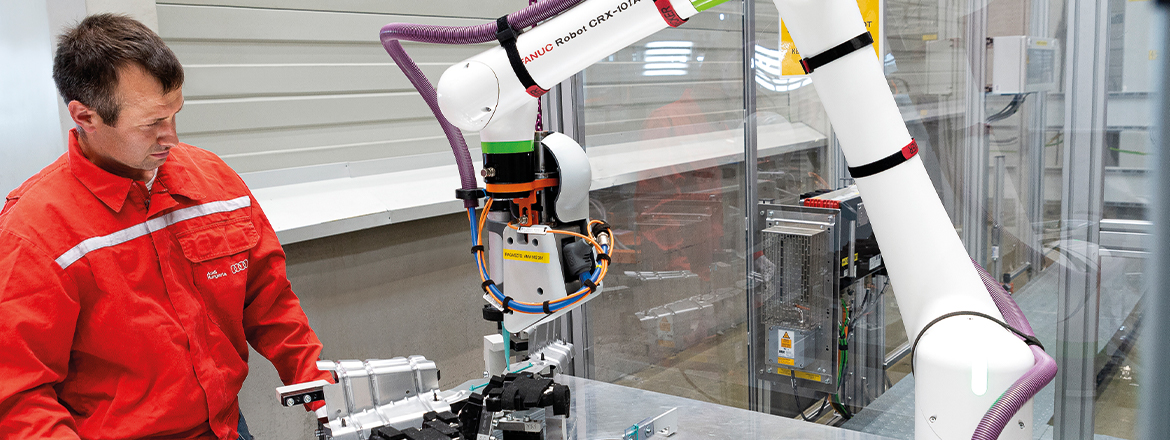
A stream of smart solutions in the Vehicle Factory
Our Experimental Engine Production Centre’s team of three engineers has worked together with bodywork specialists to develop a fully in-house camera station that provides significant support to the work of their colleagues. Each of the seven high-resolution cameras is integrated with a microcomputer, housed in a 3D-printed enclosure, and used on the bodywork PVC production line. The cameras check more than 150 points of intervention on the lower panels of the bodywork, where plugs and seals have to be inserted or removed, depending on the almost infinite number of individual customer configurations. The cameras look for any discrepancies that could lead to installation difficulties or leaks. Photos of the incoming part are taken in the cell prior to the inspection point, before the images are checked and evaluated in real time and the result is sent to the control unit. If a fault is detected, it is reported immediately to the staff member working at the next station. After an intensive testing period, the results have been clear since the cameras went live in 2021: complaints in this area have been virtually eliminated. The list of smart solutions also includes smart gloves for order picking in the Vehicle Factory. This development ensures that parts can be delivered to the installation site quickly – just-intime delivery – even with smaller stock levels. What does this mean in practice?
A pre-production logistics platform is available for sorting and preparing parts, known as ‘the supermarket’. Here, our colleague works from a collection list of more than 150 sets of parts, which they can view on atablet. Once they have selected the part they need, they scan the QR or barcode with the scanner on the back of the smart glove and the system confirms the right part has been fitted. The system has a number of advantages: it is fast, greatly reduces paper use, is costeffective, and makes work easier for our colleagues.
"The system is fast, greatly reduces paper use, is costeffective, and makes work easier for our colleagues."
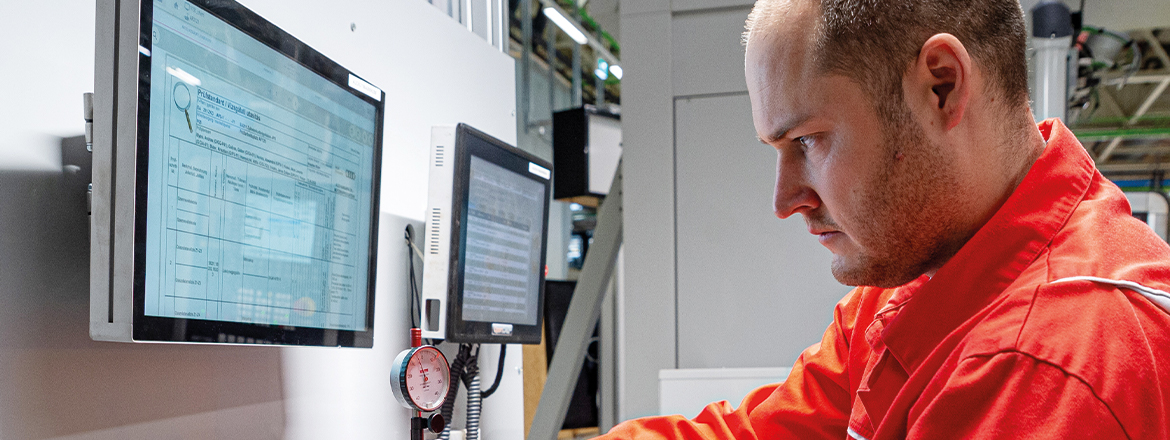
The future is sustainable, and electric!
While there is no doubt that electric drive systems are gaining ground, we continue to pay close attention to the development and sustainability of internal combustion engines, which will be with us for a long time to come. APS coating, or Atmospheric Plasma Spraying, was created with this in mind, as well as in response to increasingly stringent environmental regulations. With this technology, a layer of microporous steel, tenths of a millimetre thick, can be formed in the cylinder bores of the engine block, ensuring a good level of lubrication in the engine. This reduces internal friction and ultimately lowers CO2 emissions. Győr was the second site (after Salzgitter) in the group to introduce this innovation – which points towards a greener future – in the production of engine blocks for five-cylinder and eight-cylinder engines. In addition to the continuous development of internal combustion engines, we are also developing electric transformation and e-competencies at full speed. Series production of electric motors for Audi’s first all-electric model, the Audi e-tron, officially began on 24 July 2018. In the four years since, the headquarters in Győr – which has since become the group’s central production site for electric powertrains – has achieved a number of milestones on the road to a green future. In 2020, series production began for the new generation of e-motors, with the range of performance engines for the Audi e-tron S models powered by three electric powertrains from Győr.
Meanwhile, engineers are already looking to the future as thecompany prepares for the new generation of Premium Platform Electric (PPE) e-motors, which will complement the current portfolio that sees hundreds of thousands of e-motors produced every year. This future production process will consist of stator and gearbox component manufacturing, as well as powertrain assembly, of which the production of gearbox components will be one new factor, with an extension of competencies compared to previous e-motor production. Another new element in this process is that, for the first time in the company’s history, VR glasses and the new 3D image processing technology that comes with them have been used to design the PPE production line.
But the innovations don’t stop there, as production of the MEBeco (Modularer E-Antriebs- Baukasten – modular electric drive matrix) powertrain for the Volkswagen Group’s small electric cars is scheduled to start at a new production site in 2025. This will increase production depth, as we will also manufacture the disk pack and the rotor, and later the power electronics.
"We are developing electric transformation and e-competencies at full speed."
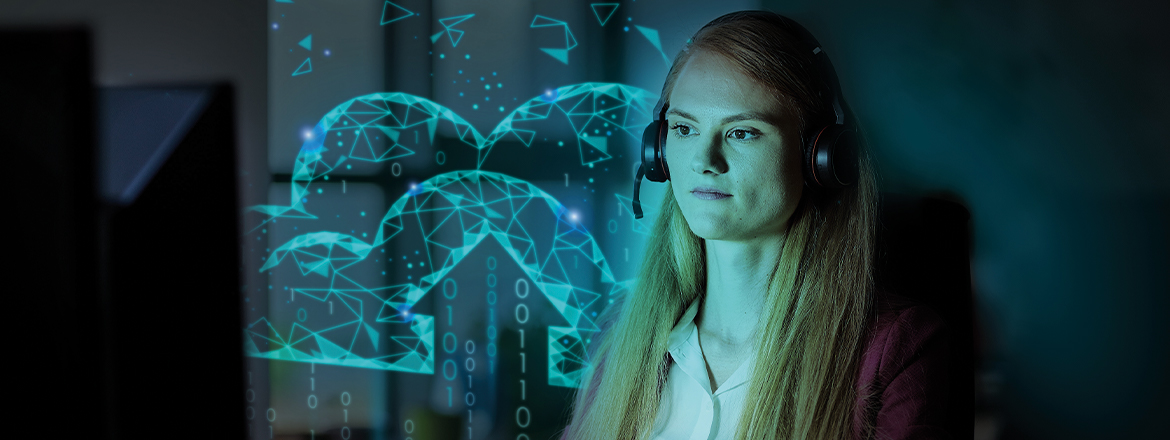
Innovative Cloud services and additional activities – the SCC’s competence-oriented services
A platform whose main objective is to support digital transformation, Kubika is a multi-tenant, containerised environment for public cloud services developed by AUDI AG on Kubernetes. In terms of its function, tenants can run their applications in the cloud in different containers, for which the Kubika infrastructure provides a reliable, flexible and secure environment in public cloud services (such as Amazon Web Services [AWS], Microsoft Azure or the Google Cloud Platform). It also offers users a rapid on-boarding option. This technology allows us to automatically deploy preconfigured environments and scale our applications without having to purchase or operate physical hardware. All this is performed quickly and securely in the cloud. The platform also provides the opportunity to use other premade services, which can also be easily installed in a matter of minutes. The Kubika team heads the Kubernetes Competence Centre. It is also a partner of the Cloud Native Computing Foundation (CNCF), and jointly develop the Kubika-O system with RedHat OpenShift. Kubika is supported and operated by the Cloud and Platform Services team.
This is not the only development in the company to support digital transformation, however. Fast and secure access to and availability of data is essential in order to take digitalisation to the next level. In order to ensure this in a future-proof and flexible way, in 2022, the employees of the IT department and the officials of the Volkswagen Group jointly planned and installed the Plant Connectivity Service, a data integration (Datalayer) service. This service makes it possible to transfer/convey data between different IT systems and platforms in a stable, secure and flexible, extensible manner, whether the systems are located in Audi Hungaria’s server centre or on one of the group’s platforms.
Among other things, the Plant Connectivity Service enables Audi Hungaria to connect to the Digital Production Platform (DPP), an innovative platform created as a partnership between Volkswagen, Amazon Web Services (AWS) and Siemens. When designing the innovative software applications based on it, the primary consideration is that they can be made available for all production sites in a fast and flexible manner. In summary, we can say that DPP provides modern and flexible cloud-based services to support and develop production processes, further increasing our efficiency.
In addition to the above activities, our IT and finance departments are also actively working in the field of process mining, with the help of a specialised partner. Process mining leads to faster and more efficient business processes that help to optimise project implementation. Regarding other projects in the SCC departments, we can highlight Vehicle Systems Controlling, which has expanded its service portfolio with innovative, forward-looking technology. This has helped the proportion of projects related to e-mobility rise to 30% in 2022. We are particularly proud of our engine manufacturing quality assurance department, which provides project management services and project-related responsibilities to the Lamborghini sports car brand.