"The bodies come from an intermediate storage area, as our main production units operate at different speeds, and this can be compensated from our intermediate storage system," begins Györgyi Csehi at the entrance point of the vehicle assembly shop. The assembly shop is also connected to the paint shop via an intermediate storage, where Dávid Romeo Ganczler informed us about the number of coatings covering the TT's bodywork. In the vehicle assembly shop, the takt time at each station is close to 100 seconds. Depending on the trim level, there are models that are either easier or more complex to assemble, so it's not all the same whether it’s an Audi Q3 Sportback or an Audi TT Roadster. When setting up the production sequence of the cars, we take into account the distance between higher-end models, such as a model for the US or the Japanese market (where safety requirements are much higher - editor's note)," adds Dávid Pozsgai.
The assembly line does not wait
The assembly line moves at a fixed speed, each work position having a starting and an endpoint. An important organisational principle is that preferably the next takt should not continue the assembly work at the place where the previous one was completed, so as to avoid any waiting time. "The series production of a model is preceded by at least two years of production planning, during which we precisely plan what will happen at which workstation and when," explains Györgyi.
"We apply the emblems on the first, i.e.. the zero section of the assembly line", continues Dávid Pozsgai, shift manager. "We place sound-insulating foams in the A-column, subsequently installing the gas sensors here, both front and rear. The doors are removed from the bodies and transported to the door assembly line, which is located next to the assembly line. This is where the vehicle receives its unique identification number, which will accompany it throughout its life. We're adding various rubber plugs to the bodywork and a lock retainer to the trunk."
The assembly shop includes a main line, integrating other pre-assembly activities in a herringbone fashion. Where we are standing right now, the door is removed at an automatic station, which then takes on a life of its own. It is transported to a preassembly line (this is where glass, cables, electronics are fitted), and the preassembled door is reconnected to the position where the fishbone is connected to the main line. Similarly, the dashboard and the chassis, for example, have their own path. After the doors have been removed, the TT will receive its side windows, and a sound-insulating cover will be glued to the roof from the inside. And all this is just the zero phase.
"Our assembly line has a non-linear layout, i.e. does not follow linear principle. From this station, for example, the bodywork goes for a cavity treatment (HRK - discussed in the previous, third part - ed.), which is an outsourced activity of the paint shop. The bodywork returns from here, but to a completely different place in the line," says Györgyi, smiling, when she notices how confused we are about where we are heading. The point is that the employees fully understand. That's why you don't see Audis with their brake lights in the front...
"It is a great challenge to assemble different models on the same assembly line in one factory. The work content varies, while each takt has nearly 100 seconds. It's a real art to balance hundreds of jobs so that all workers get an equal workload," says the head of the assembly line section, highlighting the beauty and the difficulties of work organisation.
But let’s go back to the TT, which was lost somewhere at the HRK. Oops, we were looking in the wrong place, the bodywork comes back from above, from the HRK, and it's not even a TT. "There are more and more TTs, you can feel the storm before the calm, i.e. the increased customer demand due to the upcoming discontinuation of TTs," Györgyi notes with a laugh. From here, the car is again transferred to a ground floor transport pallet. This is the so-called lower-pallet movement, as long as there is no undercarriage or wheels on the car. Then comes the suspended version, and the third mode of transport is when it can stand on its own feet and is carried by the conveyor belt with the wheels mounted. And there is a fourth one, when the car leaves the hall at full throttle. Of course, is just me adding full throttle...
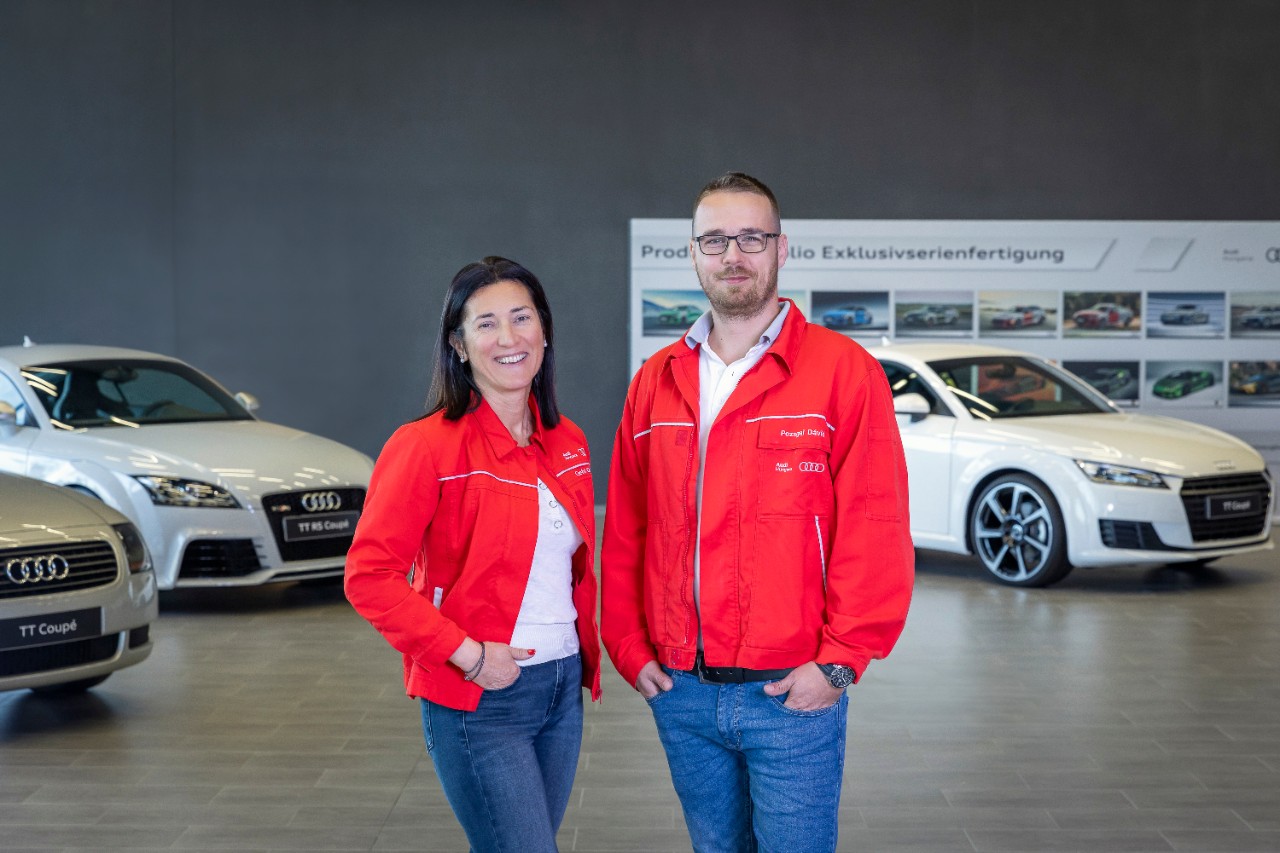
Snakes on board?
So the TT arrives from above, slides under a ground floor conveyor (squid) and we're at the first section of the assembly line (BA 1). Here, the first activity is the installation of door sealing rubbers, all kinds of fuel pipes, then the head and side airbags. The workers sit on a chair with special ergonomics, and mount the engine compartment cables from here. For a non-professional it may be surprising to know the number of kilometres of cable the TT can absorb. The "snakes" are delivered from the supplier in a bag, already prepared, and have to be distributed by the staff between the different points of the bodywork. The engine compartment is fitted with noise-abatement covers and identification labels, the car receives the pedals, and the pre-fitted dashboards arrive according to the herringbone principle. These are installed using an automatic device. From now on, the bodies will look more and more like cars. There is also and intermediate storage area here, as the speed of pre-fitting differs from that of the main line. The pre-fitted dashboards constitute a maximum of ten and a minimum of three spares.
There is a beep sound, meaning there is a break. Currently employees work in three shifts in the assembly shop. The three breaks per shift divide the working hurs into four equal parts. “Every two hours, colleagues are assigned to a different workstations, so that they don't have to perform the same activity for the entire shift," explains Györgyi. This not only reduces monotony, but is also important from an ergonomic point of view, as there are several workstations where one has to bend, stand or work reaching above the shoulder. It is important for workers not to put pressure on the same joint constantly. "Of course, this requires that all colleagues be acquainted with as many work processes as possible," adds David.
The dashboard is in place, the pedals, cables, air conditioning ducts, sound insulators, rubber plugs, the wind deflector (for Roadsters - ed.) are in place, so it’s time for the second stage.
Once again, the bodywork comes from above, with the noise-abatement layer under the carpets being the first to be applied, followed by the roof lining and the A, B and C column covers. The inside compartment starts to fill up with content, the handles, mirrors and windscreens popping into place. The latter is completed by a robot: the worker inserts the windscreen in front of the robot, from where the robot’s arms remove it and apply adhesive. The lubricated windscreen is handed out by the robot and then installed by the automatic device.
The windscreens are already installed and while I wasn't watching, the lights in the trunk door are in place as well. The front and rear lights will be installed later, in the fourth phase. Next comes the rear wing, the interior panels are fitted, the carpets are adjusted, the interior cables are installed, the extended cable loom is threaded into the engine compartment, and the appropriate cables are pulled into the roof. At this point, they breathe life into the structure and carry out an electrical test to check the electrical components that have been installed so far.
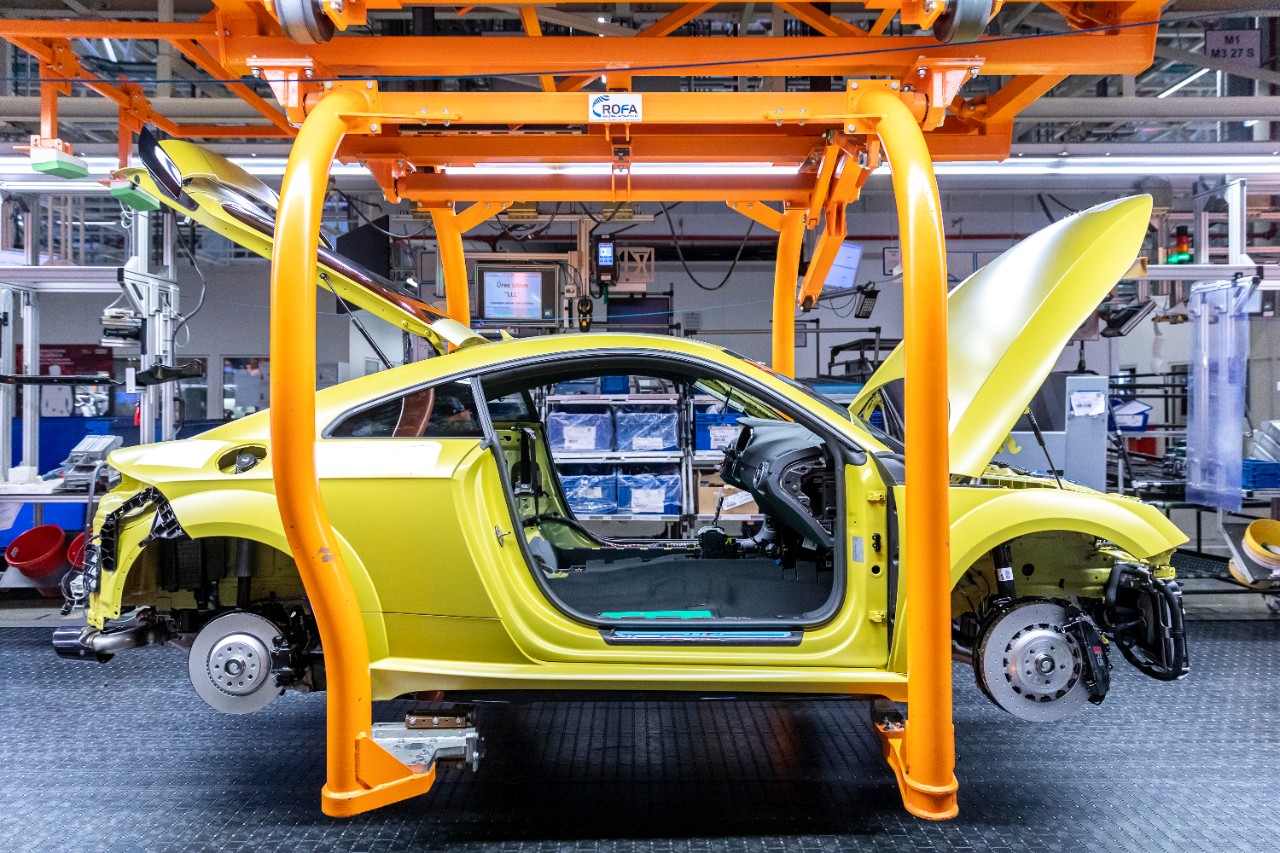
No lazing around, but wedding is
There's not a takt that's empty, there's always something going on, and this applies to the entire assembly shop, they're always working on something - be it a TT or a Q3. The bodywork is suspended again from the squid, whose path forms the letter S above us and goes to BA 3, the third line section. We're going too, because here comes the excitement: they're getting the cars ready to wed.
The wiring is not complete yet, the battery cables are arriving, and subsequently the key-sensing antennas will be installed before the wedding takes place. From a side-by-side assembly line comes the undercarriage-gearbox-engine assembly (front and rear suspension, propeller shaft, fuel tank, brake hoses, exhaust system, heat shield, etc. all in place). What does wedding mean? The chassis comes from above, and the pre-installed undercarriage-gearbox-engine comes from below. Cameras are monitoring the most critical points to ensure perfect connection, there is no intimacy, we are also watching intently. Oops, it's done, time for the next one, no time to ponder.
"As soon as the car arrives at BA 0, my colleagues will receive the order for the engine and undercarriage assembly. It takes four hours, the same amount of time the body spend on the main line. We are now halfway through production, so we need four more hours to get the car ready. In total, it takes eight hours to complete the cars in the assembly shop," explains Györgyi.
Robots bolt the undercarriage, the shock absorbers, the engine and the gearbox paw mountings, while I peek at the sideline, where the work is also exciting. The main line is almost a kilometre long, and it includes the branch lines, which jointly add up to several hundred metres.
I can't stop watching the sideline, so let's see what happens there: first the engine is mounted, and then from the other side the gearbox, the water pipes, the appropriate cables, the generator, the air conditioner, the compressor and the cooling pipes. On another line, the subframe is preassembled with the front undercarriage, and the engine-gearbox combo is placed on this. The front undercarriage is screwed together with this. Everything else, that is everything at the back, is built on this line section, that I'm admiring right now. Now the third part: the exhaust, the rear bridge, the rear suspension all arrive together. I can hardly follow the herringbones anymore, because this one is a thick fish bone, almost a marrow bone, with more tiny fishbones attached. It's crazy, I don't know where to look, everything is moving and the show is getting better and better. A Roadster is being assembled there: a battery, a rear bumper, a telephone aerial, an exhaust tip, speakers, followed by the engine compartment work, trunk and water trough covers.
"We connect the undercarriage to the body here, in a dancing takt" - (I remember David saying this) he sees that we don't understand, so he explains: "We put diagonal braces on the bottom of the Roadster, front and back, and these have to be fixed with fourteen bolts. We call it a dancing machine because you have to turn the little screwing machine as if you were dancing". Well, that’s interesting!
But the work doesn't stop here and we continue our exhaustive walk, going to the 4th line section, where the front and rear bumpers, the headlights, the front end and the lower part of the centre console are installed. At another work station, the fuel, the brake fluid, the coolant and the air conditioning are filled, the columns receive their covers, the sun-blinds are fitted and yes, the TT already has wheels.
We're now in the fifth line section, here again there is a change of conveyor, the TT wheel is fixed and the squid is moving. The seats are installed, first the rear seat, then the backrest, then the front seats, then the steering wheel, the airbag, the various design covers are fitted, the obligatory stickers are affixed in the engine compartment, the doors are fitted and the position of the doors is precisely adjusted. From the middle of the line the front end is positioned, the gaps (engine, door, trunk) are adjusted, mainly followed by control sections. The electronic test checks if everything is working perfectly. If there are no communication errors, the Audi TT will go to the undercarriage and headlight setting.
"This is where we breathe life into the cars for the first time, it's my favourite part, for me it's the most sensational place," says Györgyi enthusiastically. "It's all thoughtfully designed, it's just wonderful! On average, we assemble 2000-2200 parts, the engine is just one unit in this respect. I have not yet managed to find out exactly how many components a car consists of during my stay here - but I won't give up!" - says Györgyi as she says goodbye and Dávid returns to the assembly line with her.
And the TTs are waiting, shining and growling, for their new, meaningful and long life, which will continue somewhere in Bavaria, Anatolia, Cape Town, Chişinău, Osaka or, for the lucky ones, South Beach. But before that, they have to complete the trials and tribulations of the test track outside the hall. The RS models are road tested, followed by a seal test (they are given a monsoon spray) and then various checks are performed. Finally, they are neatly wrapped like gifts, to be unwrapped in excitement somewhere by their happy owner.