In the spirit of automation, a robotic station has been installed for the company's four-cylinder petrol engines, which places the injectors in the cylinder head. Each injector is checked by camera and photographed before insertion. Almost 680 colleagues work on these production lines, where a new R4 Otto TSI EVO2 engine leaves the production line every half a minute or so. Thanks to the project, a manual workstation was automated, reducing the number of ergonomically unfavorable workstations.
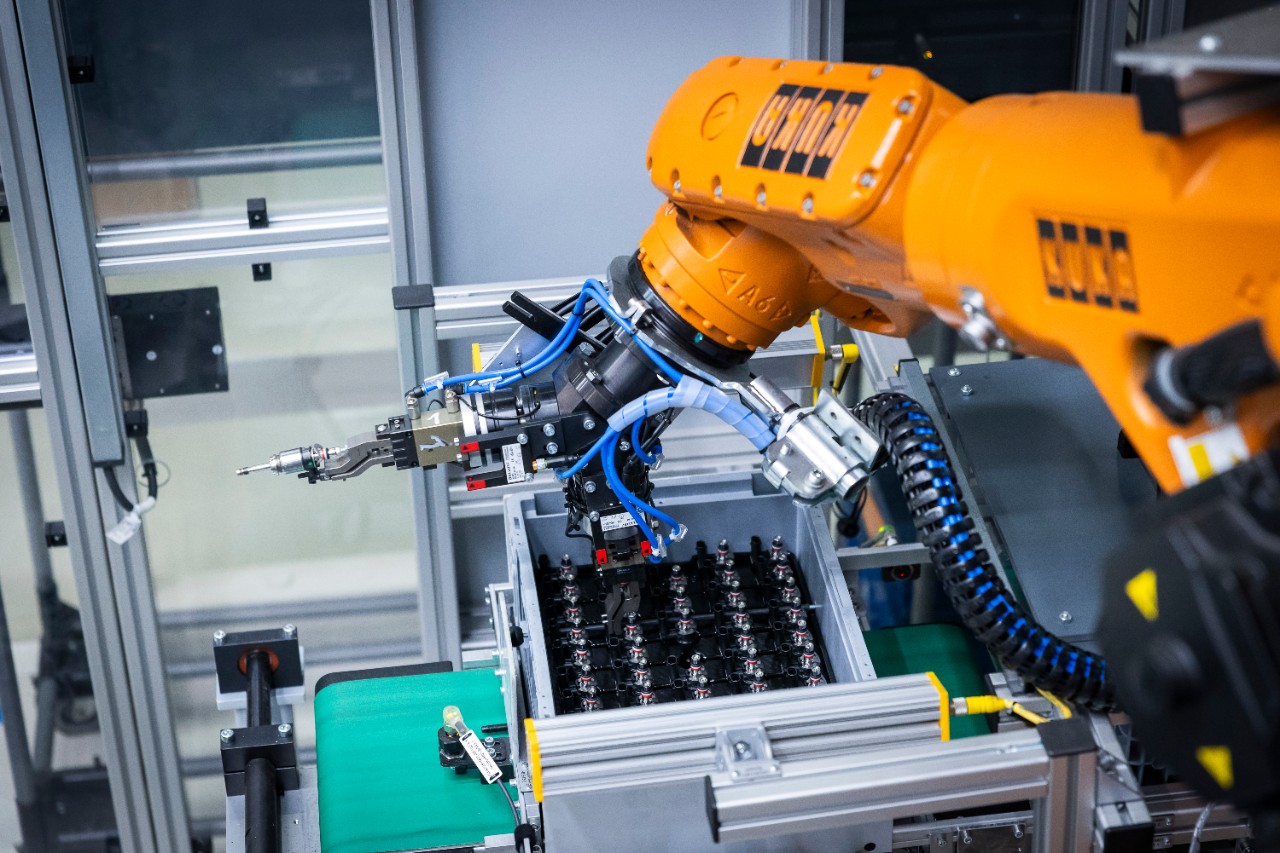
In addition, a formerly semi-automated workstation has been automated by the experts of Győr: the station, which handles 8,000 spark plugs a day, has a manipulator, a robot and a bolting station working in a single cell, which are used to place spark plugs into the three- and four-cylinder engines through an automated process. Depending on the engine type, the manipulator selects the spark plug and prepares it for the intermediate container. The robot then takes over the intermediate container and inserts the spark plugs into the spindles of the bolting station, which finally inserts and bolts the spark plug into the cylinder head. Thanks to the exchange of information between areas, a solution that is already well established in another area has been introduced in the EA211 engine assembly shop.
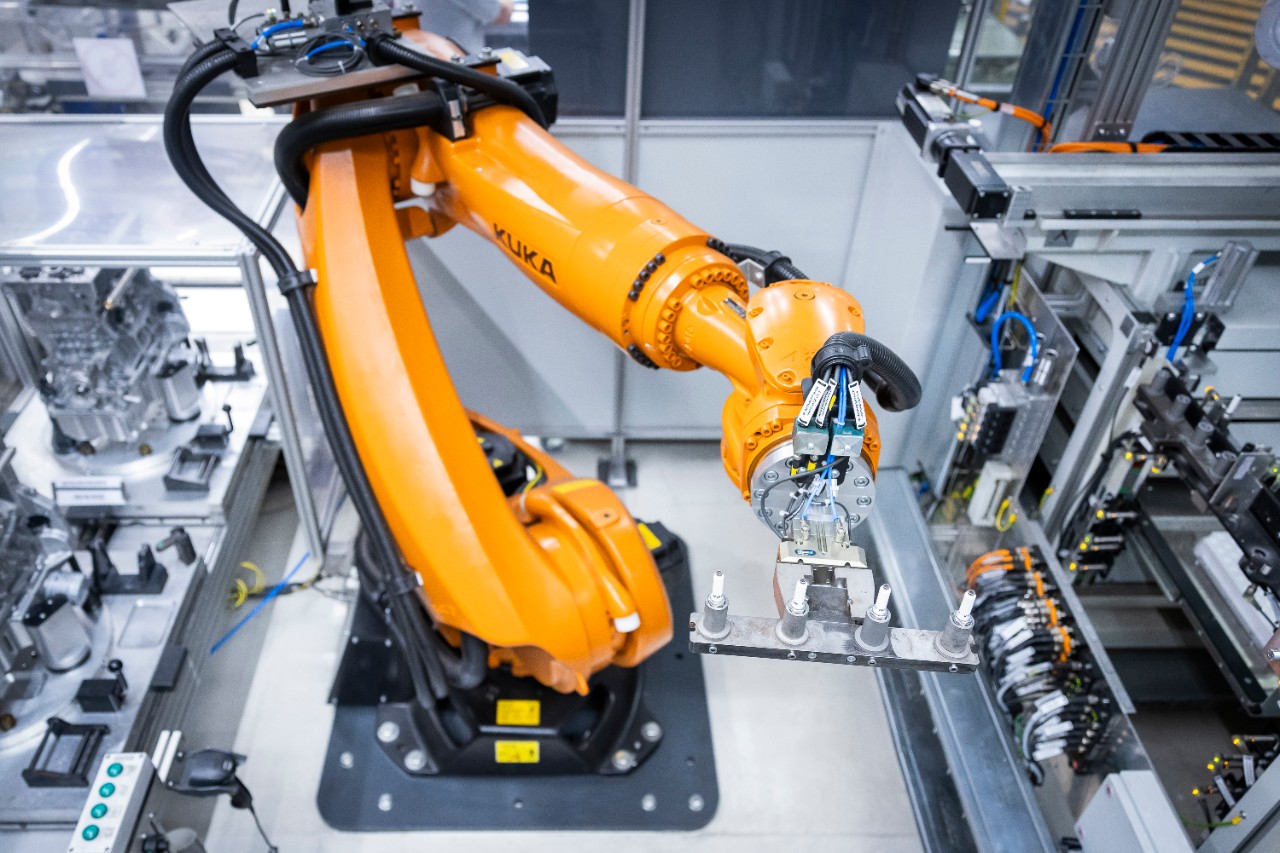
Audi Hungaria is one of the world's largest powertrain manufacturers: in 2023, its employees produced a total of 1,660,425 powertrains, of which 114,058 were electric drives. In 2023, the company started series production of the Premium Platform Electric (PPE) electric motor family, and will continue to prepare for the production of MEBeco drives in 2024.
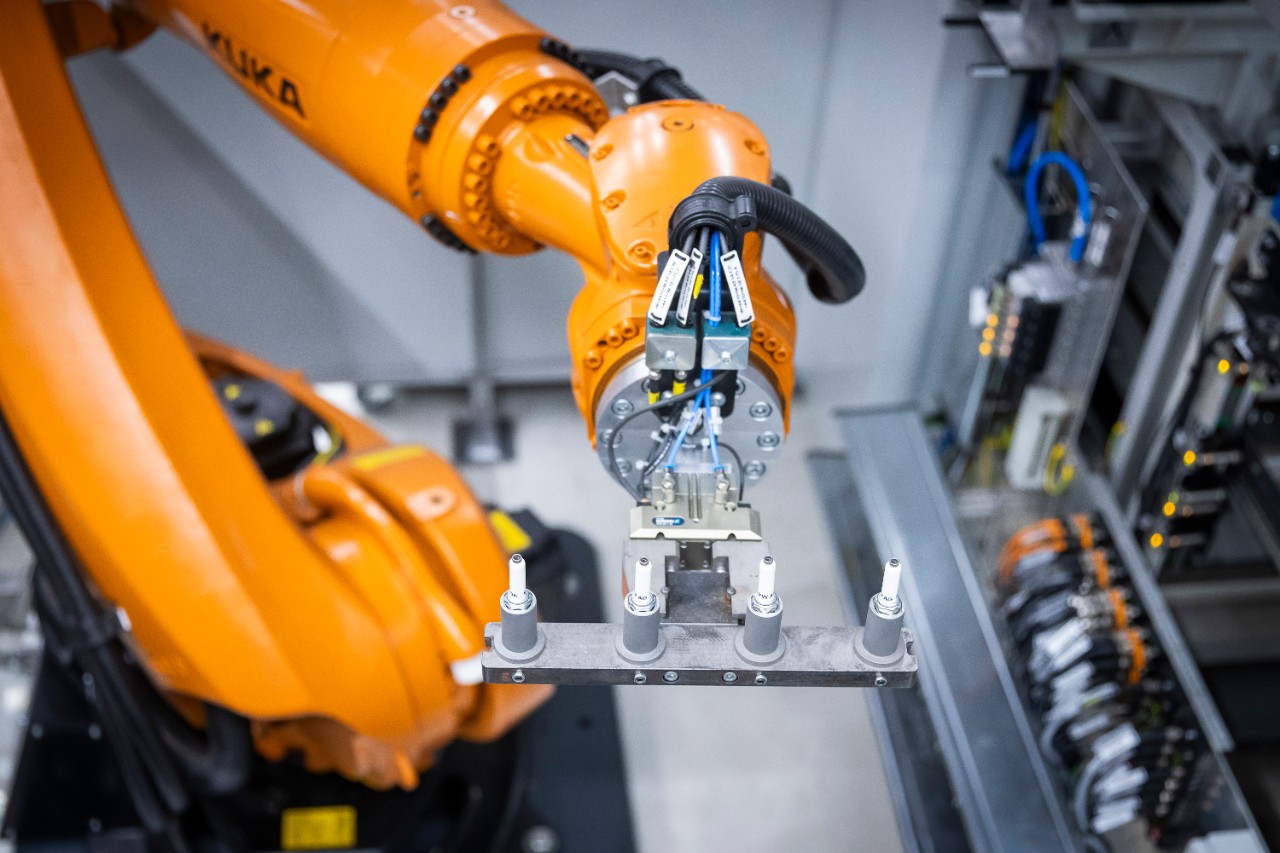