What dimensions can we talk about in terms of the production of PPE electric drives?
Csaba Imre Benke: Three new production lines have been installed to manufacture PPE drives; the stator production line consists of 28 steps, the transmission components of 15 steps, and the assembly of the drives of more than 190 steps.
How many employees are involved in production and how many electric drives are produced?
Csaba Imre Benke: In total, around 700 employees are involved in the production of PPE drives. Our production is capable of producing 2,000 drives per day for the PPE platform in three shifts. The electric drives from Győr are made for Audi and Porsche models based on the PPE platform.
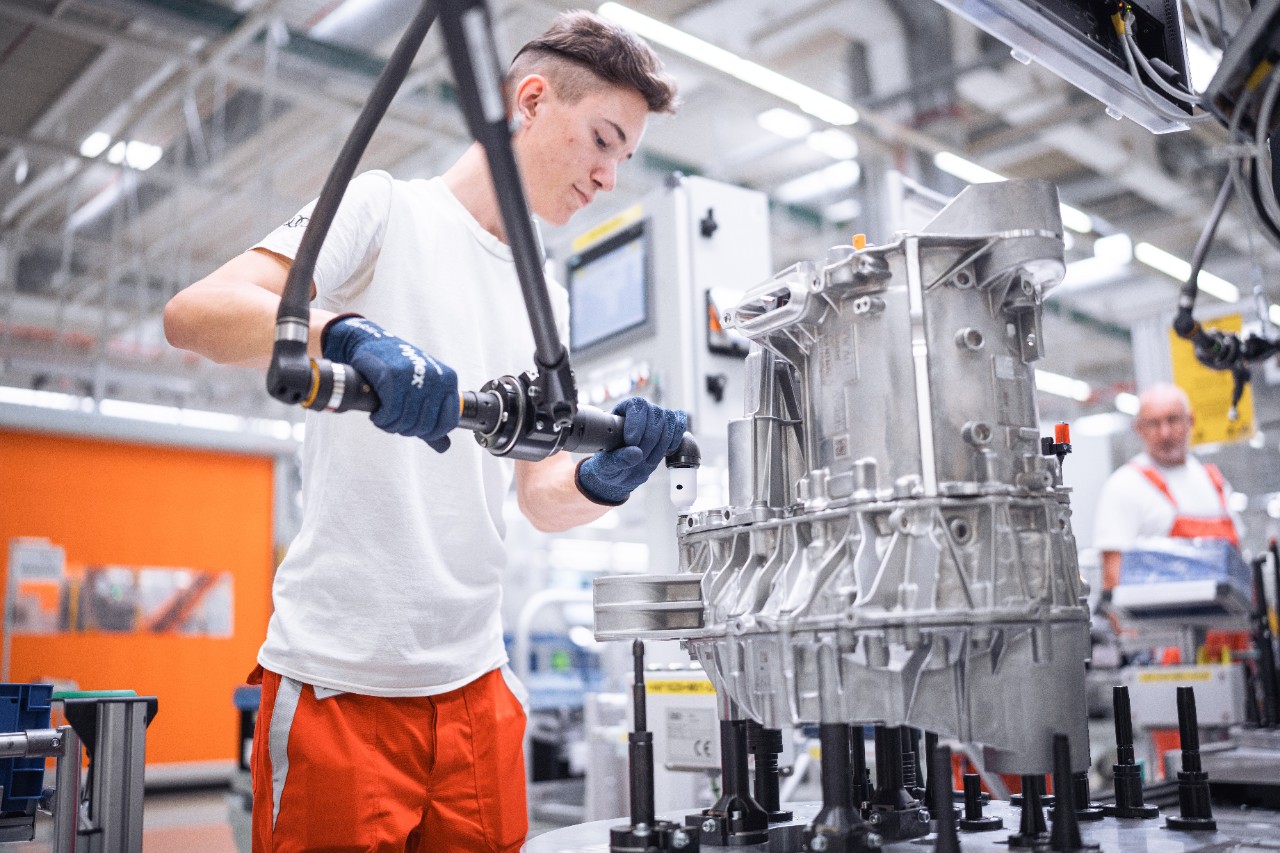
What experience does Audi Hungaria have in the production of electric drives?
Csaba Imre Benke: Of course, to produce PPE drives, we had to learn a number of processes on the new production lines, requiring around 20 days of training for our employees. However, it is important to stress that we did not start from scratch, as we have already produced more than 500,000 electric drives in Győr since 2018. By all means, this experience is of great benefit to us now. This is partly because we are gradually increasing the production depth for electric drives. As for now, we manufacture both the stator and the transmission components ourselves, but the assembly of the drives also takes place in Győr.
What are the main differences between the PPE and the previous electric drive production?
Csaba Imre Benke: In terms of production, it is safe to say that we are in a different league when it comes to PPE drives. The technological differences mean that production lines look completely different. On the PPE stator production line alone, 15 automatic winding machines bend the copper wire three-dimensionally to create the individual “hairpins”, named after their shape. The ends of the hairpins are then laser welded on two further machines. 140 meters of copper wire per stator are used, and 235 laser welding steps are required. Although in principle the production of electric drives requires fewer screw driving steps than that of internal combustion engines, more robots are needed due to the higher pressing volume. In future e-motor projects, we aim to further increase the depth of production, while also increasing automation. For example, in the case of the electric drive for the Audi Q8 e-tron, the transmission component was a purchased part, whereas in the case of the PPE, we already manufacture this part ourselves.
There are people behind the e-transformation that takes place on the production sites. How long did it take to train the employees to PPE production and what skill levels are required?
Csaba Imre Benke: The first level is a relatively simple basic training course of around two hours for colleagues working at the production line. The activity here is not significantly different from the work processes used in the production of internal combustion engines. What makes the difference is the “high-voltage sensitization training”, which is compulsory for all of our employees. Training for more complex activities requires one workday. The electronics specialists, who carry out specific activities, attend training courses lasting several days. At the highest level is the electronics specialist in charge, whose training can take up to three months, depending on their initial qualifications. In terms of workforce, we rely mainly on employees who already have experience in the world of internal combustion engines. In Győr, we have been preparing around 2,000 employees for the switch to electromobility since 2022.