The main characters in the cleanliness analysis laboratory are Audi Hungaria's experts responsible for technical cleanliness and under their professional guidance, the cleanliness testing equipment developed by the manufacturer. In the course of the manufacture and assembly of e-motors, small particles or loose burrs may impart and the e-motors may also be constantly exposed to contamination from the environment. In extreme cases, this can lead to partial or total loss of function. Our colleagues responsible for technical cleanliness work on ensuring that these situations do not occur. Metallic and non-metallic particles found on components are inspected according to stringent standards.
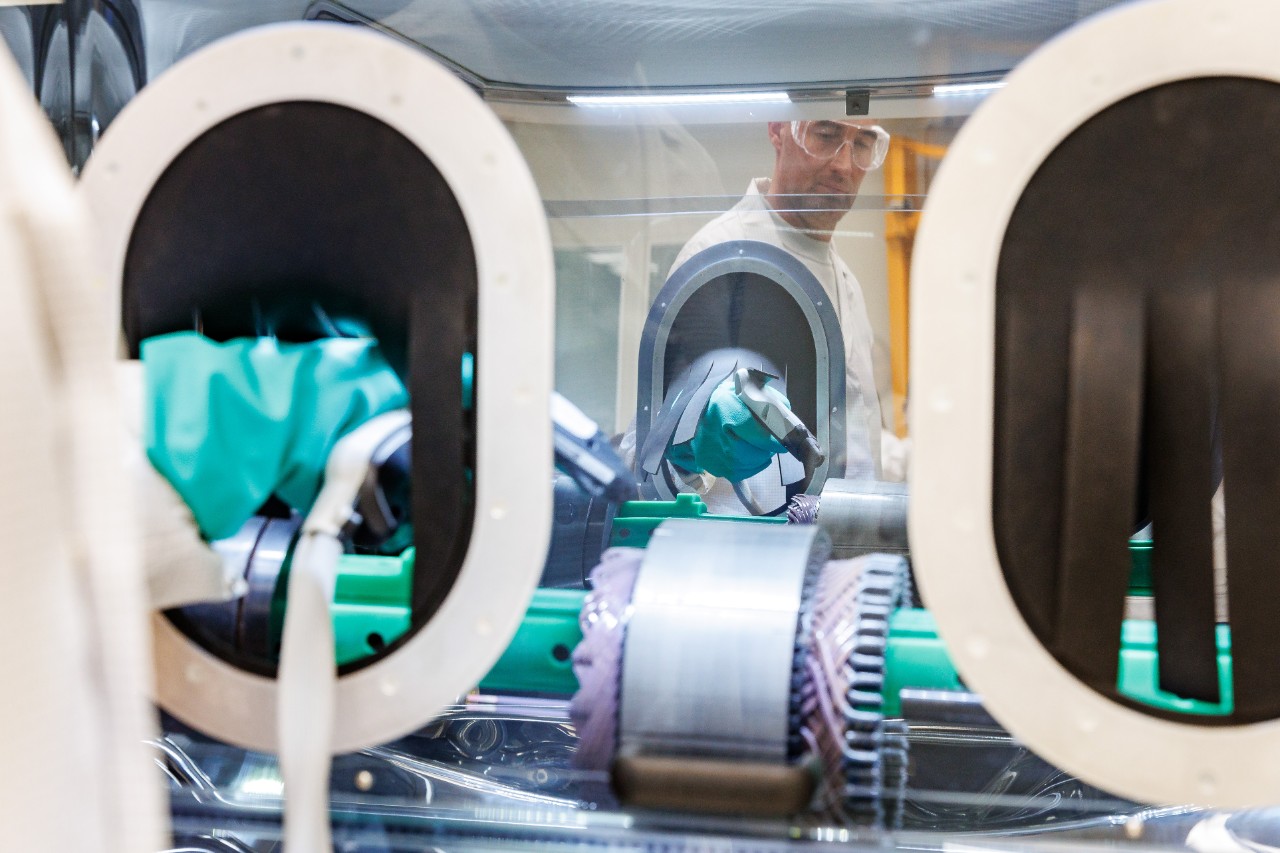
To comply with the standard, the test must be preceded by a blank value test to ensure that the technicians are convinced that the equipment is clean and therefore the cabin is fit for testing. During the blank value test, the inside walls of the cabin and all the tools involved in the test are washed and analyzed. This is essentially a complete, component-free cleanliness analysis. If everything is found to be in order, the test can go live.
In a conventional cleanliness analysis, particles are removed from the part to be tested using a special cleaning liquid and then captured by an analytical filter. After the filter is dried, the mass of the particles found on the filter is measured, and subsequently the particles are counted and categorized by size using a particle counting microscope.
There are components that cannot be tested by way of conventional liquid extraction. In such cases, a special function of the cleanliness analysis equipment should be used. When this function is activated, the removal of foreign particles from the component placed into the testing cabin is performed by ionized compressed air instead of liquid. The particles removed by blowdown stick to the pre-moistened walls of the equipment. At the end of the blowdown process, after having removed the tested component, the cabin walls are washed and any im caught in the filter is examined. This method keeps the parts dry, avoiding the need to have them scrapped, making the testing more cost-effective and environmentally optimal.
Audi Hungaria's quality management system is based on the DIN EN ISO 9001:2015 standard. The effectiveness of the quality management system has been certified by TÜV with an "excellent" rating. The company's quality is "embedded" in all areas of the company: from development through design and manufacturing to service processes. The high quality of the engines produced by the company is further enhanced by the latest testing technologies.
Audi Hungaria is one of the world's largest powertrain manufacturers: in 2023, its employees produced a total of 1,660,425 vehicle powertrains, of which 114,058 were electric drives. In 2023, the company started series production of the Premium Platform Electric (PPE) electric motor family, and will continue to prepare for the production of MEBeco drives in 2024.
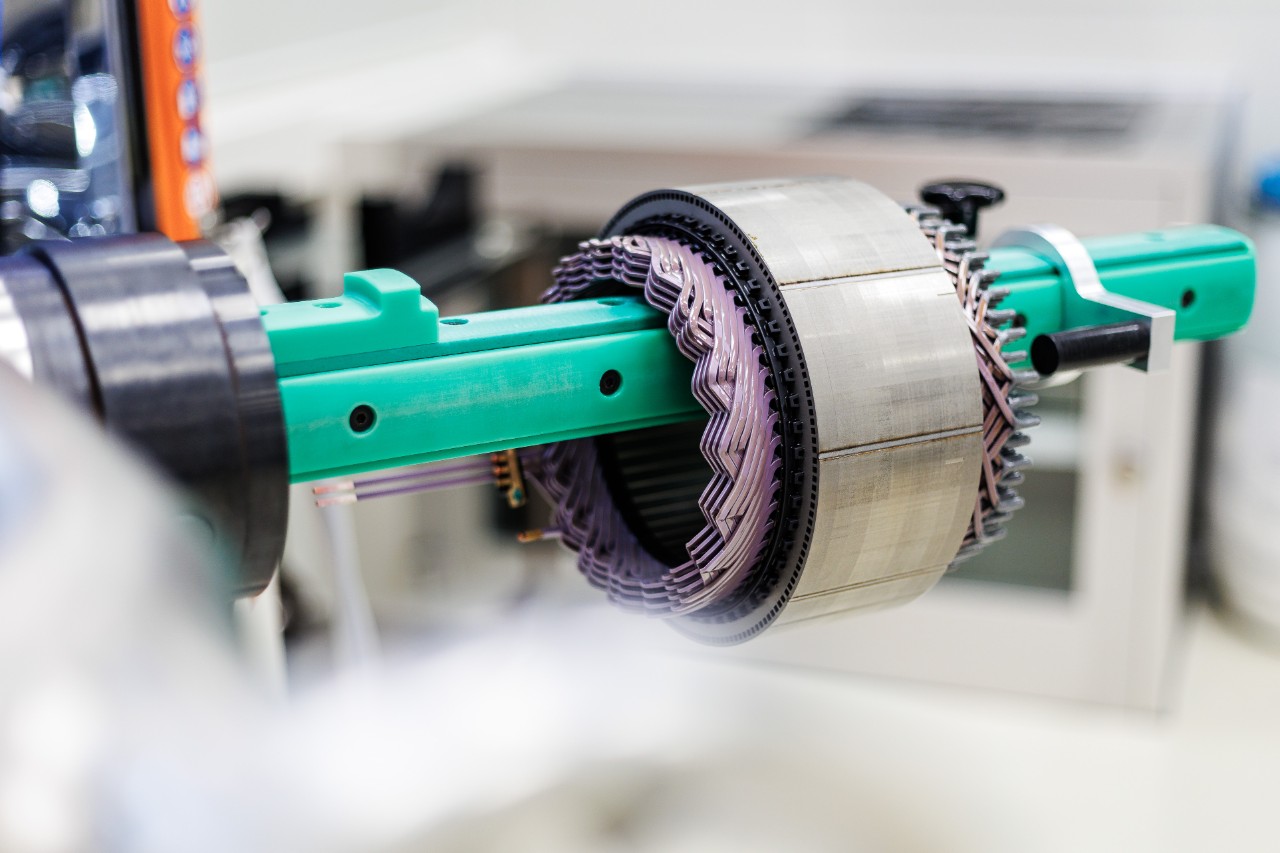
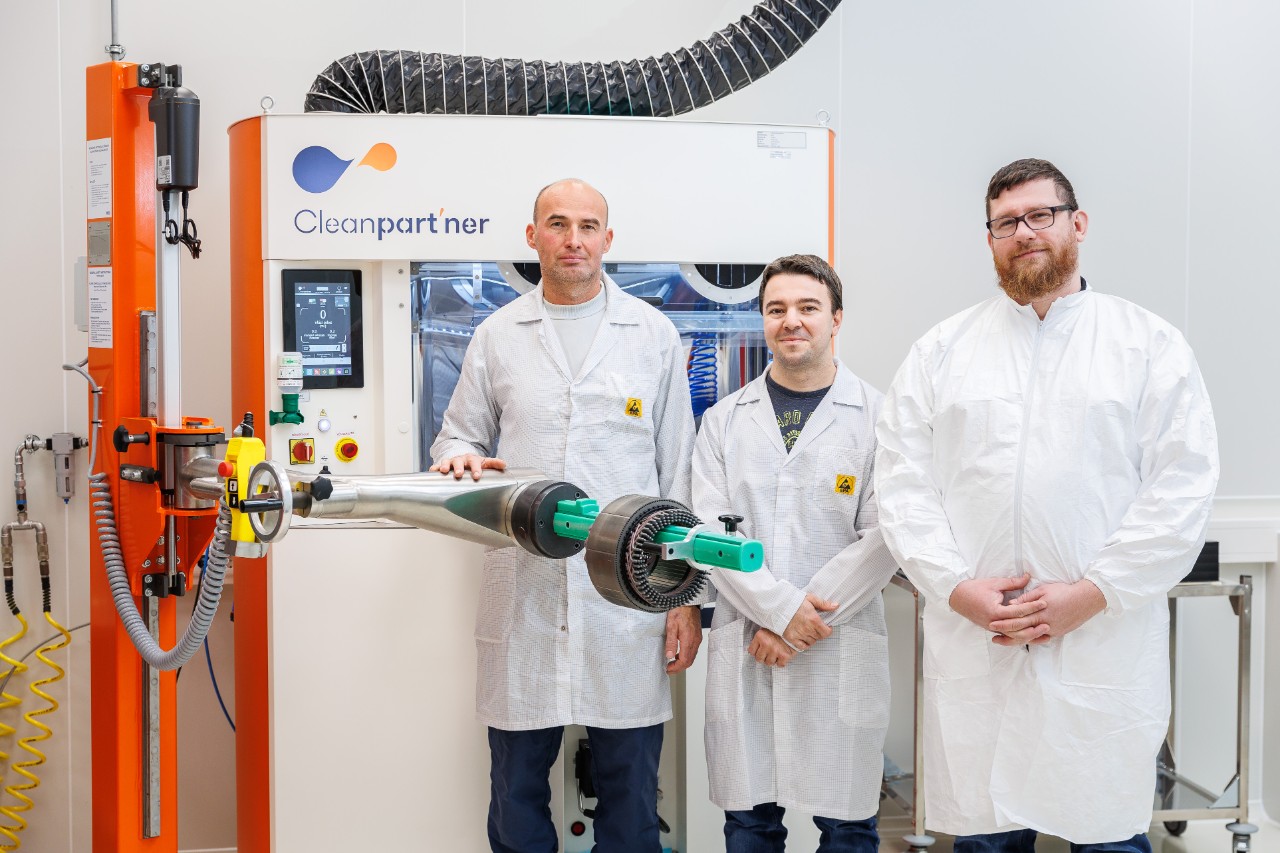