„Die Karosserien kommen aus einem Zwischenlager, denn unsere Hauptproduktionseinheiten arbeiten mit unterschiedlichen Geschwindigkeiten, die wir mit Zwischenlagern ausgleichen können“, beginnt Györgyi Csehi am Eingang der Fahrzeugmontagehalle. Die Montagehalle ist über ein Zwischenlager auch mit der Lackiererei verbunden, wo wir von Dávid Rómeó Ganczler erfahren, wie viele Farbenschichten die Karosserie des TT erhalten hat. Die Taktzeit beträgt fast 100 Sekunden an jeder Station in der Fahrzeugmontagehalle. Je nach Ausstattung gibt es einfacher und komplizierter zu montierende Modelle, es ist also gar nicht egal, ob man einen Audi Q3 Sportback oder einen Audi TT Roadster bekommt. Für höherwertige Modelle für den US-amerikanischen oder japanischen Markt soll der Abstand zwischen den Autos in der Produktionsreihenfolge berücksichtigt werden“, fügt Dávid Pozsgai hinzu (da die Sicherheitsanforderungen für solche Modelle viel höher sind – Anm. d. Red.).
Das Band wartet nicht
Die Produktionslinie bewegt sich mit einer festen Geschwindigkeit, wobei jeder Arbeitstakt einen bestimmten Anfangs- und Endpunkt hat. Es ist ein wichtiges Organisationsprinzip, dass die Montage im nächsten Takt möglichst nicht an der gleichen Stelle fortgesetzt wird, an der der vorhergehende Takt endete, damit es keine Wartezeiten gibt. „Der Serienproduktion eines Modells geht eine mindestens zweijährige Fertigungsplanung voraus, in der wir genau planen, was wann an welcher Arbeitsstation passiert“, erklärt Györgyi.
„Wir bringen die Logos auf dem ersten Bandabschnitt, d.h. Bandabschnitt Null, an“, fährt Dávid Pozsgai, Schichtmeister, fort. „In die A-Säule bringen wir schalldämmende Schaumstoffe ein, und hier werden dann die Gasdruckfedern vorne und hinten angebracht. Die Türen werden aus den Karosserien entnommen und zur Türvormontagelinie transportiert, die sich direkt neben der Produktionslinie befindet. Hier erhält das Fahrzeug seine eindeutige Identifikationsnummer, die es ein Leben lang begleiten wird. In die Karosserie werden verschiedene Gummistüpsel gebracht, und der Kofferraum wird mit der Schlosshalterung versehen.“
Die Montagehalle besteht aus einer Hauptlinie, in die andere Vormontagetätigkeiten fischgrätenartig integriert sind. Wo wir jetzt stehen, wird die Tür durch eine automatische Station abgenommen, und sie wird dann ein getrenntes Leben führen. Sie wird zu einer Vormontagelinie transportiert (wo Glas, Kabel und Elektronik installiert werden), und die fertige Tür wird dann wieder an die Hauptlinie angeschlossen, wo ihr Fischgräte mit der Hauptlinie verbunden wird. Ähnlich nimmt das Armaturenbrett, bzw. das Fahrgestell einen separaten Weg. Nach der Demontage der Türen bekommt der TT seine Seitenscheiben, und auf das Dach wird von innen eine Schallschutzverkleidung geklebt. Und das alles war nur Phase Null.
„Unsere Produktionslinie hat keine regelmäßigen Linien, sie folgt nämlich keinen linearen Prinzip. Von dieser Station geht die Karosserie zum Beispiel zur Hohlraumkonservierung (HRK – wie im dritten Teil dieses Artikels erwähnt – Anm. d. Red.), die eine ausgelagerte Tätigkeit der Lackiererei ist. Von dort kommt sie zurück, aber an einer ganz anderen Stelle wieder in die Linie“, sagt Györgyi und lächelt, als sie merkt, dass wir keine Ahnung haben, wo wir sind und wohin wir von hier aus gehen. Das Wichtigste ist, dass die Mitarbeitenden es genau wissen. Deshalb sehen wir auch keine Audis mit Bremslichtern vorne...
„Es ist eine große Herausforderung, im Werk verschiedene Modelle auf demselben Band zu montieren. Der Arbeitsinhalt ist ja unterschiedlich, und jeder Arbeitstakt dauert doch etwa 100 Sekunden. Es ist eine echte Kunst, Hunderte von Arbeitsstationen so auszubalancieren, dass alle Mitarbeitenden die gleiche Arbeitsbelastung haben“, sagt die Bandabschnittleiterin und hebt die Schönheit und die Schwierigkeiten der Arbeitsorganisation hervor.
Aber zurück zu unserem TT, der irgendwo bei der HRK verloren gegangen ist. Ups, wir haben an der falschen Stelle nachgeschaut, eine Karosserie kommt von oben aus der HRK zurück, aber es ist kein TT. „Es gibt immer mehr TTs, man spürt den Sturm vor der Ruhe, d.h. die erhöhte Kundennachfrage aufgrund des bevorstehenden Auslaufs der TTs“, bemerkt Györgyi lachend. Von hier aus wird das Auto wieder auf eine Skidpalette gelegt. Das nennt man „Skidtransport“, solange kein Fahrgestell oder keine Räder am Auto sind. Dann kommt die aufgehängte Lösung, und die dritte Transportart ist die, bei der das Auto auf seinen eigenen Füßen steht und mit befestigten Rädern auf dem Förderband transportiert wird. Soweit ich weiß, gibt es auch noch eine vierte Transportmethode, bei der das Auto mit Vollgas die Halle verlässt. Natürlich füge nur ich das Vollgas in Gedanken hinzu...
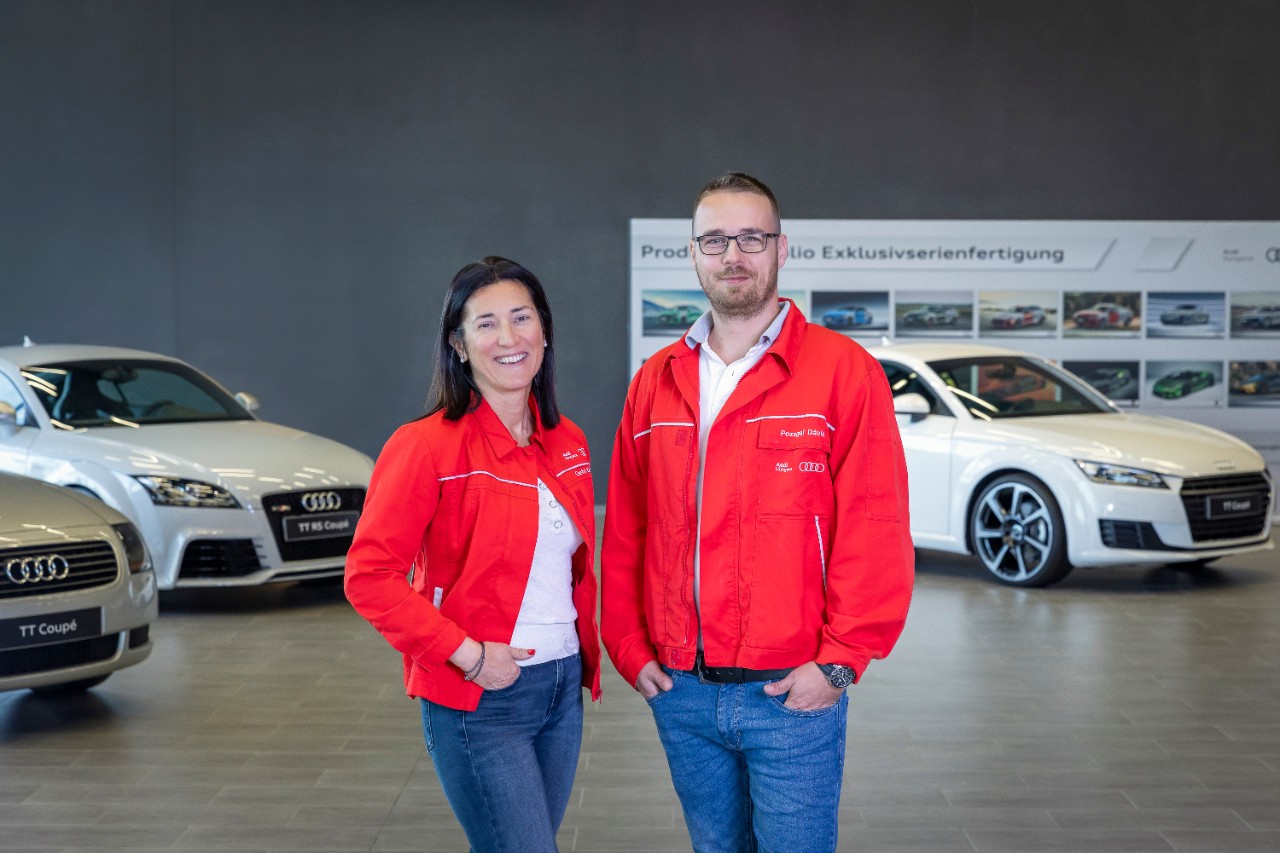
Schlangen an Bord?
Der TT kommt also von oben, ein Skid wird unter ihm geschoben und wir befinden uns schon auf Bandabschnitt eins (BA 1). Hier werden als erstes die Türdichtungen montiert, dann werden die Kraftstoffschläuche sowie die Kopf- und Seitenairbags eingebaut. Die Mitarbeitenden sitzen auf einem speziellen Ergonomiestuhl, von dem aus sie die Kabel im Maschinenraum montieren. Für Uneingeweihte mag es überraschend sein, wie viele Kilometer Kabel der TT schlucken kann. Die „Schlangen“ werden vom Zulieferer in einer Tüte vorbereitet geliefert, und die Mitarbeitenden sollen sie an den verschiedenen Stellen der Karosserie auslegen. Der Motorraum wird mit geräuschdämpfenden Abdeckungen und Kennzeichnungsschildern versehen, das Auto erhält die Pedale, und die vormontierten Armaturenbretter kommen nach dem Fischgrätenprinzip an. Diese werden durch ein automatisches System eingebaut. Von nun an sieht die Karosserie mehr und mehr wie ein Auto aus. Auch hier gibt es ein Zwischenlager, denn die Geschwindigkeit der Vormontage unterscheidet sich von der Hauptlinie. Es gibt maximal zehn und mindestens drei vormontierte Armaturenbretter in Reserve.
Ein Tonsignal ertönt jetzt, da eine Pause kommt. Im Moment arbeitet man in drei Schichten in der Montagehalle. Die drei Pausen pro Schicht teilen die Arbeitszeit in vier gleiche Zeitabschnitte ein. „In jedem Zyklus, d.h. alle zwei Stunden werden die Kollegen an eine andere Arbeitsstation versetzt, damit sie nicht die ganze Schicht über die gleiche Arbeit machen müssen“, erklärt Györgyi. Dies ist nicht nur wichtig, um die Monotonie zu verringern, sondern auch aus ergonomischer Sicht, da es mehr Arbeitsstationen gibt, an denen man über die Schultern arbeiten, sich bücken oder stehen muss. Es ist wichtig, dass die Mitarbeitenden nicht immer das gleiche Gelenk belasten. „Das setzt natürlich voraus, dass alle Kollegen so viele Arbeitsabläufe wie möglich kennen“, fügt David hinzu.
Das Armaturenbrett ist montiert, die Pedale, Kabel, Klimakanäle, Geräuschdämpfer, Gummistüpsel und der Windabweiser (für die Roadster – Anm. d. Red.) sind an ihrem Platz; jetzt kann die zweite Phase beginnen.
Wieder kommt die Karosserie von oben ab, die Geräuschdämpfungsschicht unter den Teppichen wird als erste angebracht, gefolgt vom Dachhimmel und den Abdeckungen der A-, B- und C-Säulen. Der Innenraum beginnt sich mit Inhalt zu füllen, Griffe, Spiegel und Windschutzscheiben werden angebracht. Die Windschutzscheibe wird von einem Roboter fertiggemacht: der Mitarbeitende legt sie vor den Roboter, von wo aus die Roboterarme sie aufnehmen und mit Klebstoff bestreichen. Die bestrichene Windschutzscheibe wird vom Roboter ausgegeben und dann vom automatischen System eingebaut.
Die Windschutzscheiben sind also eingebaut, und als ich nicht hingesehen habe, wurde auch die Lampe in der Kofferraumklappe bereits eingebaut. Die Vorder- und Rückleuchten werden später (in der vierten Phase) eingebaut. Als Nächstes kommt der Heckflügel, die Innenverkleidungen werden angebracht, die Teppiche werden angepasst, die Innenraumkabel werden installiert, die ausgelegte Kabelpeitsche wird in den Motorraum eingefädelt, und die passenden Kabel werden in das Dach eingezogen. Jetzt wird das System beseelt und ein elektrischer Test wird durchgeführt, um die bis dahin eingebauten elektrischen Komponenten zu überprüfen.
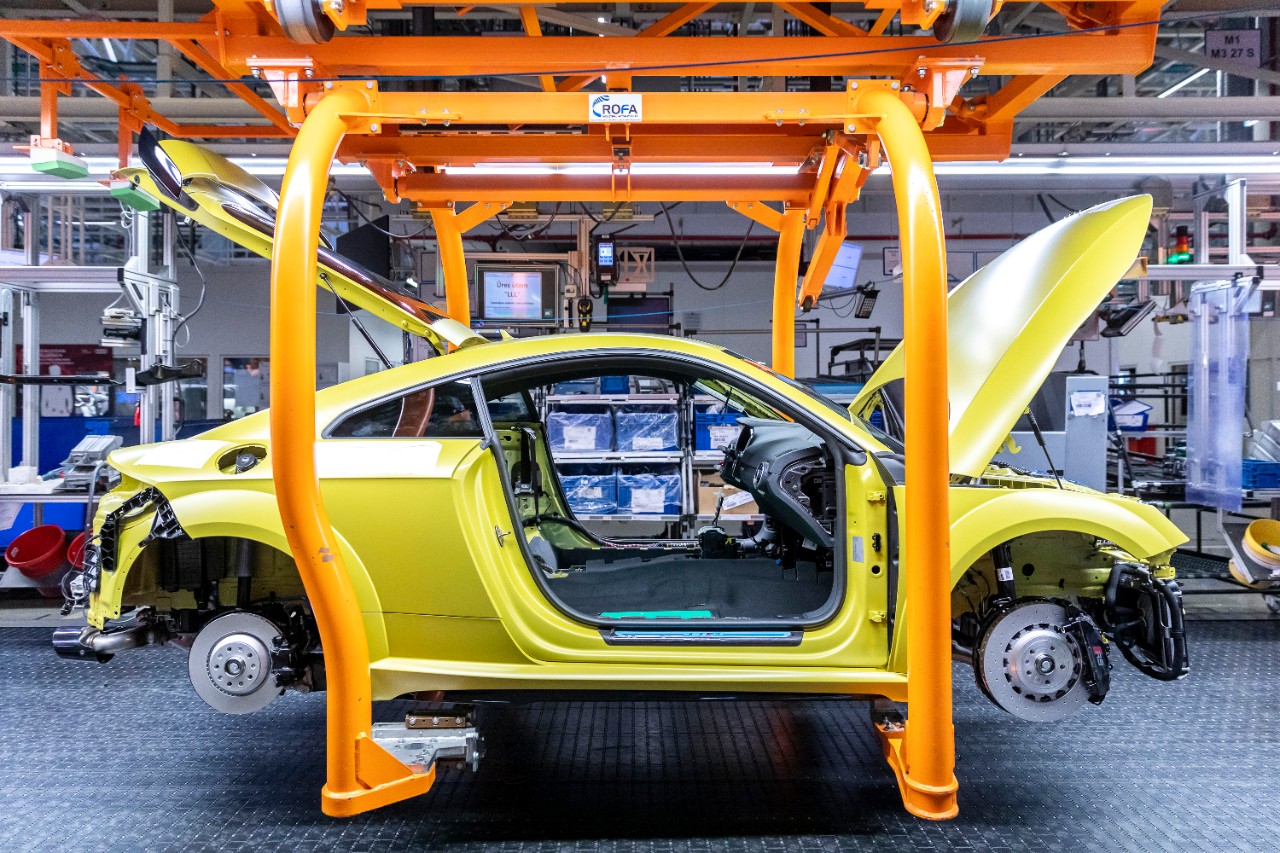
Keine Zeit für Gammelei, die Hochzeit kommt
Es gibt keinen einzigen leeren Takt, etwas ist immer los in der ganzen Montagehalle, man fasst immer was an – sei es TT oder Q3. Die Karosserie wird vom Skid wieder aufgehängt, und sie nimmt einen S-förmigen Verlauf über uns als sie zu BA 3 (d.h. Bandabschnitt 3) geht. Wir gehen mit, denn jetzt kommt die Aufregung: die Autos werden für die Hochzeit vorbereitet.
Die Verkabelung ist noch nicht abgeschlossen, die Batteriekabel kommen noch, und dann werden die Antennen für den Schlüsselsensor angebracht, bevor die Hochzeit geschieht. Von einer seitlichen Vormontagelinie kommt die Baugruppe von Fahrgestell, Getriebe und Motor (Vorder- und Hinterradaufhängung, Kardanwelle, Kraftstofftank, Bremsschläuche, Auspuffanlage, Hitzeschild usw. sind bereits montiert). Was ist die Hochzeit? Die Karosserie kommt von oben, und die vormontierte Baugruppe von Fahrgestell, Motor und Getriebe kommt von unten. Kameras überwachen die kritischsten Punkte, um eine perfekte Verbindung zu gewährleisten: es gibt keine Intimität, wir schauen genau hin. Hoppla, fertig, hier kommt das nächste Fahrzeug, keine Zeit zum Nachdenken.
„Sobald das Auto auf BA 0 eintrifft, erhalten meine Kollegen den Auftrag für den Zusammenbau von Motor und Fahrgestell. Das dauert vier Stunden, und die Karosserie verbring genauso lange Zeit auf das Hauptlinie. Wir haben jetzt die Hälfte der Fertigung hinter uns, d.h. wir brauchen weitere vier Stunden, um das Auto fertigzustellen. Insgesamt dauert es acht Stunden, bis die Autos in der Montagehalle fertig sind“, erklärt Györgyi.
Roboter schrauben das Fahrgestell, die Stoßdämpfer, die Motor- und Getriebeböcke an – ich werfe einen Blick auf die Seitenlinie, wo die Arbeit ebenfalls spannend ist. Die Hauptlinie ist fast einen Kilometer lang, und dazu kommen noch die abzweigenden Seitenlinien, die sich insgesamt ebenfalls über mehrere hundert Meter erstrecken.
Ich komme von der Seitenlinie nicht los, also schauen wir mal, was passiert: Zuerst wird der Motor montiert, dann von der andere Seite werden das Getriebe, die Wasserschläuche, die entsprechenden Kabel, der Generator, die Klimaanlage, der Kompressor, die Kühlleitungen angebracht. Auf einer anderen Linie wird der Hilfsrahmen mit dem vorderen Fahrgestell vormontiert, auf dem die Motor-Getriebe-Kombination montiert wird. Damit wird das vordere Fahrgestell zusammengeschraubt. Alles andere, was sich auf der Heckseite befindet, wird also auf diesem Bandabschnitt aufgebaut, den ich gerade bewundere. Nun zum dritten Teil: die Auspuffanlage, die hintere Brücke und die hintere Aufhängung kommen schon zusammengebaut. Ich kann die Fischgräten kaum folgen, denn es ist eine dicke Fischgräte, fast eine Markgräte, an die sich weitere kleine Gräten anschließen. Es ist verrückt, ich weiß gar nicht, wo ich hinschauen soll, alles ist in Bewegung und das Programm wird immer besser. Da wird ein Roadster gefertigt: Batterie, hintere Stoßstange, Telefonantenne, Auspuffende, Lautsprecher werden montiert, gefolgt von Motorraumarbeiten, Kofferraum- und Wassertrogabdeckungen.
„Wir verbinden hier das Fahrgestell mit der Karosserie, in einem Tanztakt“ (das hat vielleicht Dávid gesagt), er nun sieht, dass wir das nicht verstehen, also erklärt er: „Wir bringen Diagonalstreben vorne und hinten an der Unterseite des Roadsters an, die mit vierzehn Bolzen befestigt sind. Wir nennen es Tanztakt, weil wir die kleine Schraubmaschine die ganze Zeit so drehen müssen, als ob wir tanzen würden.“ Was es alles gibt!
Aber die Arbeit hört nicht auf, und wir setzen unseren anstrengenden Spaziergang fort, indem wir zum Bandabschnitt vier gehen, wo die vorderen und hinteren Stoßstangen, die Scheinwerfer, das Frontend und der untere Teil der Mittelkonsole montiert werden. An einer anderen Station werden Kraftstoff, Bremsflüssigkeit, Kühlmittel und die Klimaanlage gefüllt, die Säulen erhalten ihre Abdeckungen, die Sonnenblenden werden montiert und ja, der TT bekommt hier auch Räder.
Wir befinden uns nun auf Bandabschnitt fünf, auch hier wird die Transportmethode gewechselt, die Räder des TT werden befestigt und der Skid läuft weiter. Die Sitze werden eingebaut, zuerst die hinteren, dann die Rückenlehnen, dann die vorderen Sitze, das Lenkrad wird zusammen mit dem Airbag montiert, die verschiedenen Designabdeckungen werden angebracht, die obligatorischen Aufkleber werden im Motorraum angebracht, die Türen werden montiert, und ihre Position wird ebenfalls genau eingestellt. In der Mitte der Linie werden das Frontend und die Spaltmaße (Motor, Türen, Kofferraum) angepasst, und es folgen nun hauptsächlich Kontrollphasen. Ein elektronischer Test wird durchgeführt, um sicherzustellen, dass alles einwandfrei funktioniert. Wenn es keine Kommunikationsfehler gibt, geht der Audi TT zur Fahrgestell- und Scheinwerfereinstellung.
„Hier werden die Autos zum ersten Mal beseelt, das ist mein Lieblingsteil, die sensationellste Stelle für mich“, schwärmt Györgyi. „Alles ist sehr durchdacht, es ist einfach erstaunlich! Im Durchschnitt bauen wir zwischen 2000 und 2200 Teile ein, und der Motor ist dabei nur eine Einheit. Aus wie vielen Teilen ein Auto genau besteht, habe ich in meiner Zeit hier noch nicht herausfinden können – aber ich gebe nicht auf“, sagt Györgyi zum Abschied und Dávid geht mit ihr zurück zum Band.
Und die TTs warten glänzend und brummelnd auf ihr neues, erlebnisvolles und langes Leben, irgendwo in Bayern, Anatolien, Kapstadt, Mădăraș, Osaka oder South Beach (für die Glücklichen). Zuvor müssen sie aber noch die Prüfungen auf der Teststrecke außerhalb der Halle bestehen. Die RS-Modelle werden auf der Autobahn gefahren, dann folgt eine Dichtprüfung (sie werden unter einem Monsunregen getestet) und dann kommen noch verschiedene Überprüfungen. Zum Schluss werden sie wie Geschenke schön eingepackt, um dann von ihren glücklichen Besitzern mit Spannung ausgepackt zu werden.