Wie alle anderen Bereiche, wird auch der Karosseriebau in Győr auf dem neuesten Stand der Technik betrieben. Mehr als 2.000 Maschinen arbeiten hier in einer Schicht. Die Schweißzangen werden elektrisch betrieben – d.h. sie arbeiten schneller, genauer, zuverlässiger, leiser und sind leichter zu bedienen als die bisherige servopneumatische Lösung. Der Maschinenpark wird durch Spann-, Positionier-, Clinch- und Bördelgeräte sowie Schweißstationen für spezielle Aufgaben abgerundet.
Die Karosserien des TT werden auf einer Fläche von ca. 85.000 Quadratmetern gefertigt. Auf beiden Seiten der Hauptlinien schweißen Robotergruppen einzelne Bauteile wie: Bodengruppen, Radhäuser und Längsträger zusammen. An die Karosserie, die Schritt für Schritt aus der Stirnwand, Rückwand, den Säulen, Seitenteilen und dem Dach entsteht, werden zuletzt die Motorhaube, der Kofferraumdeckel und die Seitentüren angefügt. Eine Karosserie wird in 3,7 Stunden hergestellt, davon entfallen zwei Stunden auf die Bearbeitung und 1,7 Stunden auf die Bewegung.
Aufgrund der geringen Kundennachfrage wird die Fertigung derzeit mit einem kleinen Team von knapp 50 Personen pro Schicht durchgeführt. Wenn man die Halle betritt, sieht man nur in einzelnen Bereichen Kollegen und Kolleginnen arbeiten. Die Mitarbeitenden bauen die beiden TT-Modelle, das Coupé und den Roadster, schrittweise auf den einzelnen Anlagen, wie es das Programm vorsieht. Dennoch ist es beeindruckend zu sehen, wie viele Roboter startklar auf die Karosserien warten, damit sie ihre Arbeit automatisch erledigen können.
Linien Aufbau bzw. Unterbau 1, 2, 3, 4
Unser Begleiter Attila Schler gibt einen kurzen Überblick über das, was uns erwartet: „Hier haben wir die vorderen Seitenwände, das Einstellen der Rahmen, dort drüben das Clinchen und Nieten, und dort kommt das Dach hinzu“, zeigt er nach rechts. „Danach werden die aufgehängten Elemente in die Audi TTs eingebaut. Die verschiedenen Linien haben die Bezeichnungen Aufbau bzw. Unterbau 1, 2, 3, 4 usw.“
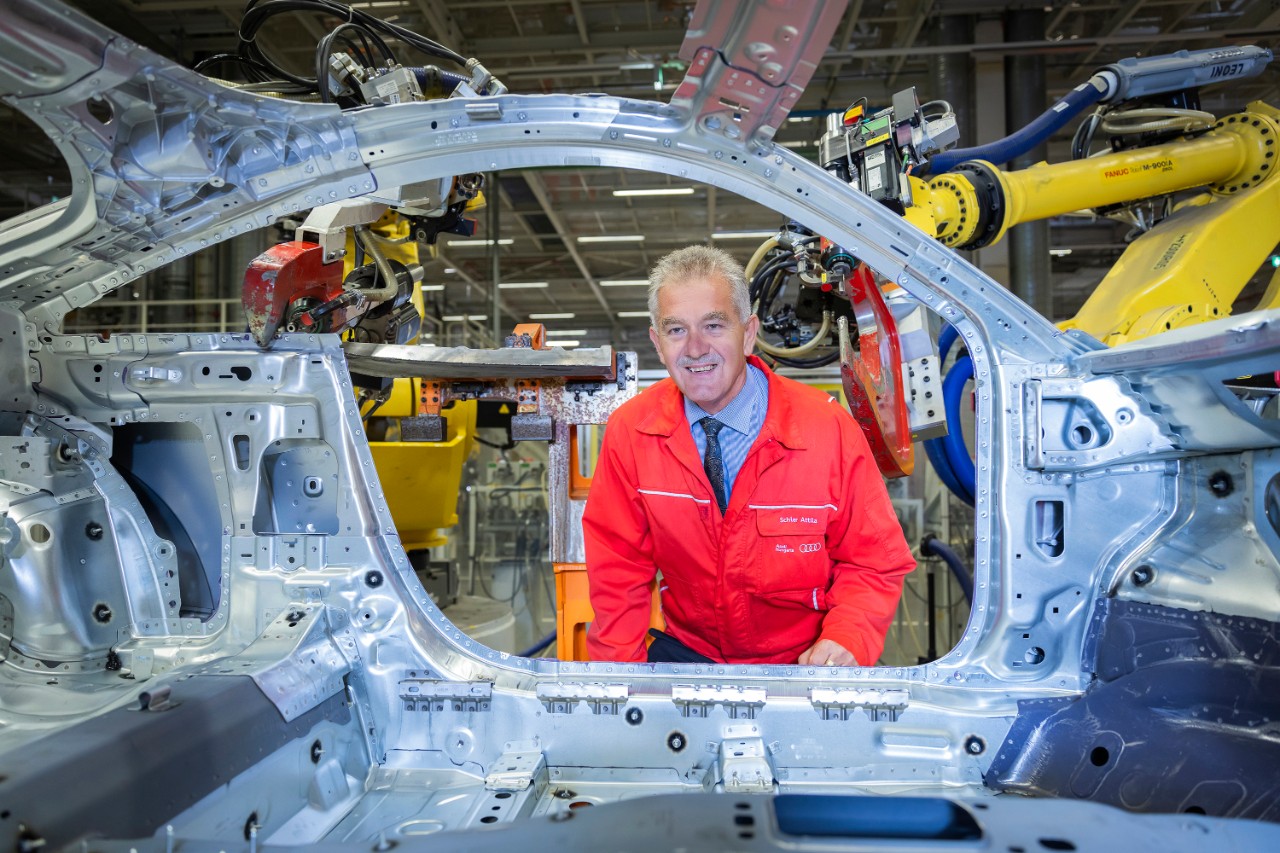
Der Aufbau ist aus Aluminium und die meisten Komponenten kommen aus dem Presswerk, das wir bereits kennengelernt haben. Aber es gibt auch noch einige Bauteile, die nicht in Győr hergestellt werden. Der Unterbau ist aus Stahl, größtenteils aus warmgeformtem hochfestem Stahl, aber auch ein wenig Aluminium ist im Materialmix auch enthalten.
Aufgrund der kurzen Zeit, die uns zur Verfügung steht, gehen wir nicht den gesamten Fertigungsablauf bis hin zur Entstehung des Audi TT.
Wir kommen im Bereich Unterbau an und zwar bei der Finish-Linie 4, wo eine 100-prozentige Maßkontrolle, eine Sichtprüfung und Lichtbogenschweißen durch die Mitarbeitenden sowie automatische Anlagen die hervorragende Audi-Qualität garantieren. Danach kommen wir an einem manuellen Arbeitsplatz vorbei, wo die Fußraumplatte für den Roadster vormontiert wird. Bei der Linie 3 „werden der bodennahe Unterbau, die Stirnwand und die Radhäuser aufgenommen“ erzählt uns der Begleiter. Linie 3 umfasst eine TT-spezifische Zusatzlinie 3A, bei der auch Aluminiumelemente am Unterbau montiert werden. Der Grund dafür ist, dass der Unterbau des TT in die Unterbaulinie der A3 Limousine und des A3 Cabriolets (gebaut in Győr zwischen 2013 und 2019) integriert ist.
In der Zwischenzeit erhalte ich die Notizen unseres Begleiters mit einer unendlichen Aufzählung der Verbindungsarten, die beim TT eingesetzt werden. Haltet euch fest, hier kommen ein paar technische Details: 128 fließlochformende Schrauben FSD, 3033 Schweißpunkte, 1,9 Meter MAG-Schweißen, 1149 selbstschneidende Nieten, 78,8 Meter Festigkeitsklebung, 5,1 Meter Laserschweißen, 44 Vollnieten, 207 Clinchen, 1,8 Meter Falzen und sechs SB. Verbindungstechniken an den Aufbauten: 112 Clinchen, 1149 selbstschneidende Nieten, 35,3 Meter Kleben, 22,5 Meter Falzen. Es gibt also noch eine Menge zu lernen, wenn man ein Auto bauen will! Vor allem, wenn es um einen TT geht, denn bei diesem besteht allein der Kasten aus über tausend Bauteilen. Und wie sieht es mit dem Roadster aus? Bei der Fertigung der Karosserie des Audi TT Roadsters kommen 16 verschiedene Verbindungstechniken zum Einsatz, vom Widerstandspunktschweißen an 2963 Arbeitspunkten bis hin zu den 77,16 Meter langen hochfesten Klebungen. Wo immer möglich, werden Schweißen und Kleben in einem Arbeitsgang durchgeführt, wodurch Zeit, Kosten und Gewicht eingespart werden. Am Ende jeder Linie prüft ein separates Messgerät die Abmessungen. Die Kollegen der Instandhaltung überwachen und verringern durch verschiedene Entwicklungen ständig den Energieverbrauch, egal ob es sich um Strom oder Druckluft handelt.
Ewiger Bund der Platten
Wir befinden uns bereits bei der Linie Unterbau 1, wo die vordere Bodenplatte, die Längsträger und die hintere Bodenplatte miteinander verbunden werden, von hier aus geht das Auto zum Schweißen und erhält seine Fahrgestellnummer.
Die Fertigung richtet sich nach dem Fertigungsplan, der aus Ingolstadt kommt und in das Werksmanagementsystem eingespeist wird. Die hintere Bodenplatte ist der Vorreiter, sie ruft die anderen Bauteile ab. Alles, was spezifisch ist, wird hier im Presswerk hergestellt. Wenn der Unterbau fertig ist wird er über ein Hängefördersystem auf die andere Seite bewegt und am Anfang der Linie Aufbau 1 heruntergefahren. Die A-, B-, C-Säulen bilden die innere Seitenwand, sie werden in Aufnahmelinien nach dem Fifo-Prinzip (first in, first out – Redakteur) in die Autos eingebaut, erklärt Attila.
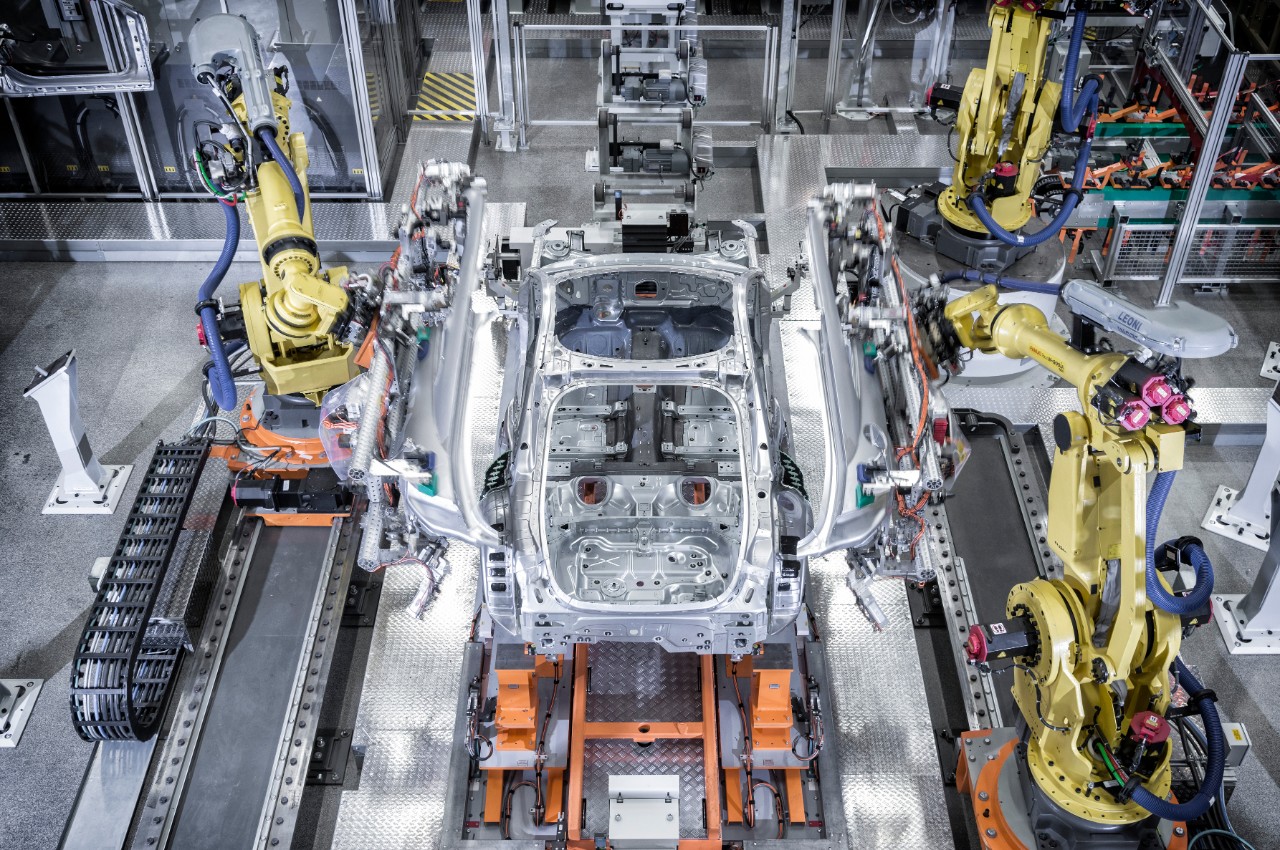
In der Halle Aufbau treffen wir einen Kollegen, der, wie wir erfahren, gerade Wasserkanal und Lampengehäuse fertigt. Er legt die Bauteile in eine Geo-Vorrichtung und die Anlage verbindet die Teile durch clinchen oder sie verwendet je nach Modell eine andere Verbindungstechnik. Bei der Fertigung des TT liegt der Automatisierungsgrad im Karosseriebau bei ca.70 Prozent. Es gibt nur wenige manuelle Arbeitsstationen, aber ein Beispiel für Handarbeit ist die Fertigung von Dachverbindungen.
Heutzutage, am Ende der Lebensdauer des Produkts ist die Stückzahl gering, erklärt unser Begleiter. Früher wurden 40–50 Karosserien pro Schicht gefertigt, in Spitzenzeiten sogar 60–70 – heute werden nur noch 17-18 Autos pro Schicht montiert. Dazu mussten wir eine rentable Mitarbeiterzahl schaffen. Es gibt ein kleines Team, das zuerst die kleineren Einheiten zusammenbaut und dann von Abschnitt zu Abschnitt weitergeht. Zuerst werden z.B. die Seitenwände und die zugehörigen Teile hergestellt bis der Unterbau aus dem anderen Ende der Halle eintrifft.
Wir konnten auch im Hut dabei sein, wie der Unterbau die innere Seitenwand in der Aufbau-Linie 1 erhält. Der Roadster unterscheidet sich vom Coupé: Er hat den Überrollbügel im Frontscheibenrahmen, der zusammen mit der hinteren Beifahrerschutzeinheit aus Ingolstadt kommt.
Auf der nächsten Linie (Aufbau 2) wird die äußere Seitenwand eingebaut, diese wird durch den so genannten „Spannrahmen“-Framer in Position gebracht. Dieser spannt und richtet die Seitenteile zum Unterbau. Anschließend setzen die Roboter Geoschweißpunkte, um den Unterbau mit den Seitenteilen präzise zu verbinden. Darauf folgt eine 100-prozentige geometrische Kontrolle, um die perfekte Passform der Türen, Kotflügel und Motorhaube zu gewährleisten.
Das Dach wird mit einem Laserverfahren aufgeschweißt. Auf beiden Seiten löten zwei Roboter das Dach an die Seitenwände. Die exakte Position des Daches, wie Tiefe, Position von vorne nach hinten und zur Seite, wird durch die sogenannte „Glocke" gewährleistet. Dieser Vorgang ist sehr schnell und effizient, aber auch sehr empfindlich auf äußere Einflüsse. Das Dach muss fast fugenfrei an die Seitenwände anschließen. Stellt euch vor, die beiden Schweißnähte werden von den beiden Robotern in etwa 25 Sekunden parallel gelötet. Eine beachtliche Leistung!
Am Ende der Linie stehen bereits die fertigen Karosserien: Man kann erkennen, welche Teile aus hochfestem Stahl und welche aus Aluminium sind. Natürlich ist die Arbeit noch lange nicht beendet: Es folgen noch strenge Kontrollen. Die Festigkeit der Schweißverbindungen wird bei der Montage des Unterbaus mit Ultraschall geprüft, und bei der fertigen Karosserie kontrollieren speziell geschulte Mitarbeitende vor der Lackierung die Fügungen und die Oberflächen auf Mängel. Aber wir haben bereits die Form eines Autos vor uns, das muskulöse Heck und das perfekt anmutende Gesicht des TT sind deutlich zu erkennen, aber die streng wirkenden Matrix-LED-Scheinwerfer lassen sich noch auf sich warten. Unsere Reise geht weiter, und wir danken Attila Schler für seine Begleitung und seine Expertise. Auf geht‘s zur Lackiererei, über die wir im nächsten Teil unserer Serie berichten werden.