Es gibt keine Mitarbeitenden im Fahrzeugwerk, die nicht mit ihm in Berührung kommen. Wie ich erfahren habe, gibt es keinen Takt im Werk, in dem man nicht mit dem Audi TT oder dem Audi TT Roadster entlang der Linie etwas zu tun hätte, wenigstens für eine kurze Berührung, ein Streicheln. Aber wir wollen nicht voreilig sein, beginnen wir am Anfang der Linie.
Das Audi-Werk in Győr ist riesig, kein Wunder, es ist das größte Motorenwerk der Welt. Alle Motoren auch für den Audi TT werden vor Ort gebaut, und das war bereits früher so, als noch nicht alle Phasen der Montage bei uns stattfanden. Seit 2013 wird jedoch fast jedes Teil des TT in Győr hergestellt – natürlich gibt es eine ganze Reihe von Bauteilen, die wir von Zulieferern beziehen, aber auch unter ihnen sind einige aus Győr und dem Komitat Győr-Moson-Sopron. Mit der Motorenproduktion, Fertigungsplanung, Entwicklung, Qualitätskontrolle und dem Testen befassen wir uns jetzt nicht, wir folgen der Hauptströmung. Wir besuchen vier Bereiche: Presswerk, Karosseriebau, Lackiererei und Fahrzeugmontage. Über unsere Erfahrungen und Erkenntnisse berichten wir in vier Artikeln. Bleibt dran, es wird spannend!
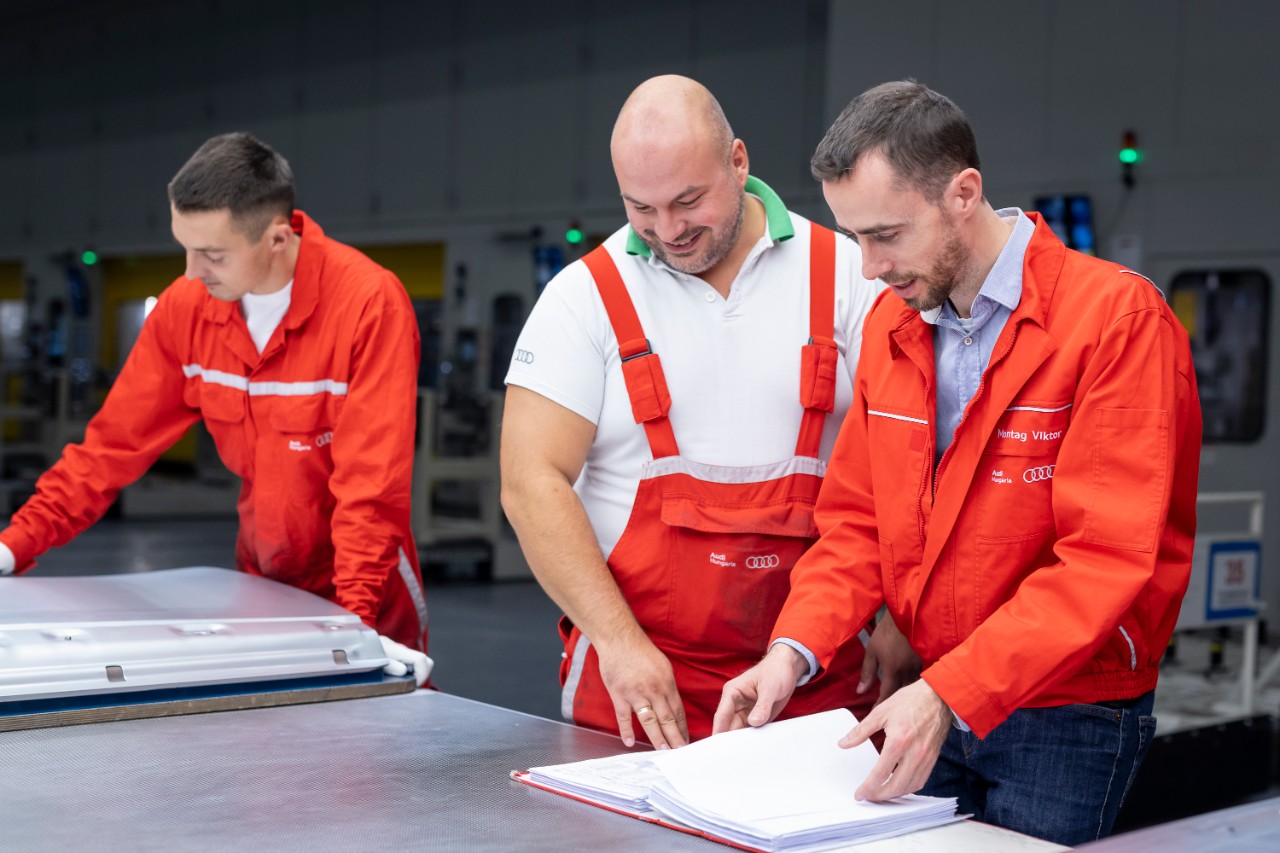
Presswerk: Wo das Blech zum Bauteil wird
„Die Aluminiumrollen mit einem Gewicht von 5 bis 9 Tonnen und die Stahlrollen mit einem Gewicht von bis zu 33 Tonnen kommen per Bahn in einem externen Lager in Dorog an, von wo aus sie mit Mulden-Lastkraftwagen ins Werk transportiert werden“, erklärt Viktor Montag, Fertigungsplaner im Presswerk, die ersten Schritte des Entstehungsprozesses. Die mit dem Kran abgehobenen Rollen werden zu einem Zwischenarbeitsbereich bewegt, wo sie geschnitten und dann an drei Bereiche weitergegeben werden. Einige von ihnen werden nach Bratislava transportiert, wo die Blechstücke auf einer Presse, ähnlich wie in Győr, bearbeitet werden, und auch an den Werkzeugbau und natürlich an das Presswerk in Győr, wo das Leben der Audi TT Sportwagen beginnt. Die gepressten Bauteile werden in einem Fertigwarenlager gelagert, und der Karosseriebau entnimmt hier die entsprechenden Teile nach seinem Bedarf. „Für den TT verarbeiten wir hauptsächlich Aluminium, der Anteil von Aluminium beträgt etwa 80 Prozent. Alles, was außen am Auto ist, ist aus Aluminium. Alles, was aus Stahl ist, ist meist innen, so das Bodenblech, die Radhäuser, bestimmte Strukturbauteile“, erzählt uns Viktor Montag über die Details.
Es ist laut im Presswerk, vor allem, wenn man in die Nähe der beiden Schuler-Maschinen kommt: Die Schneidemaschine leistet 70 Millionen Hübe und die Presse rund 25 Millionen Hübe in ihrem Lebenszyklus, beide wurden 2013 installiert. Früher kamen die lackierten Karosserien aus Ingolstadt, damals für die erste und später für die zweite Generation des TT. Für die dritte Generation, die 2014 debütierte, wurden die Karosserieteile bereits im Presswerk in Győr gefertigt.
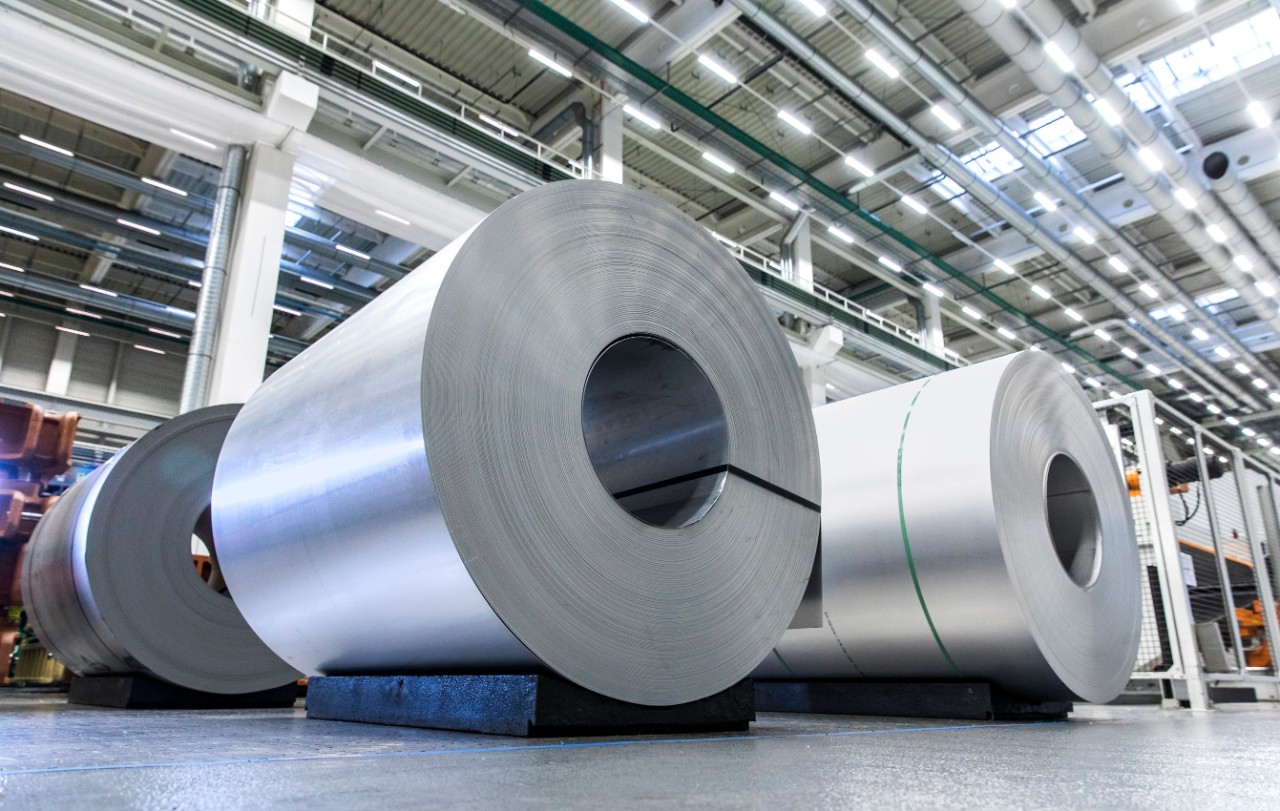
Im Presswerk liegt der Schwerpunkt auf dem Gleichgewicht: Das Produkt soll die richtige Qualität mit dem geringstmöglichen Anteil an Schnittabfall haben. Die eingehende Materialmenge beträgt etwa 40.000 Tonnen, etwa die Hälfte davon wird in der ersten Runde technologischer Abfall. Dieser wird natürlich wiederverwendet. Der Aluminium Closed Loop ist ein geschlossener Kreislauf für Aluminium beim Unternehmen, so dass der wertvolle Rohstoff in gleicher Qualität in den Kreislauf zurückgeführt wird.
Im Presswerk, wo rund 180 Personen an den Radhäusern und Seitenwänden für den TT arbeiten, werden die vorbereitenden Arbeiten neben dem großen Kran mit 8-Tonnen-Flurförderzeugen durchgeführt. Wir kommen an der Blechgrube vorbei, wo der reibungslose Fluss der Stahl- oder Aluminiumbleche im Kontrast zu der kontinuierlichen Bewegung der Rollen durch Unterbrechung, Verlangsamung und Ausgleich gewährleistet wird. Im Werk Győr gibt es 106 TT-Presswerkzeuge (für Tiefziehen, Schneiden und Stanzen pro Bauteil, in einem Hub können auch mehrere Bauteile gefertigt werden) – für alles das richtige Werkzeug. Ein Teil der Werkzeuge wird in dem benachbarten Werkzeugbau gefertigt. Es gibt sehr viele davon, ein großer Teil wird nach dem Abschied vom TT Ende November recycelt, einige Werkzeuge werden aber auch weiterhin nachgefertigt. Dabei werden noch jahrelang TT-Bauteile für die Werkstätten gepresst. Natürlich nicht in solchen Stückzahlen...
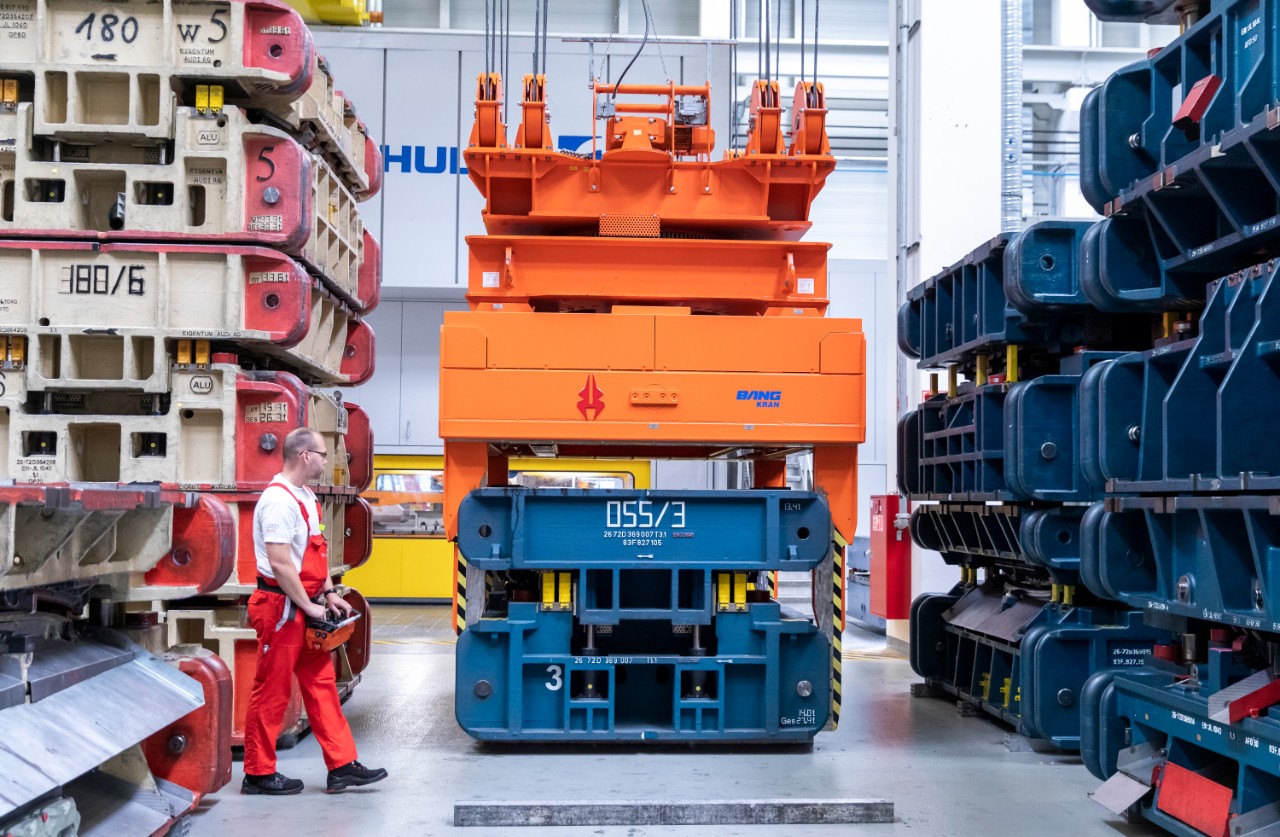
Tonnen über uns, Tonnen um uns herum
Wir kommen an der Presse mit einer Gesamtkraft von 81.000 Kilonewton, also 8100 Tonnen, an. Die Bewegung der Bauteile ist robotergesteuert, aber in der Vormontage arbeiten auch Menschen: Sie heben die Werkzeuge mit dem Kran an. Über uns bewegen sich Werkzeuge im Wert von Hunderttausend Euro und mit einem Gewicht von 15-20-40 Tonnen, von einem Mitarbeiter wie eine Spielzeugkonsole ferngesteuert.
Die Positionierung des Blechs in der Presse ist ein spektakulärer Vorgang: Ein Roboterpaar bereitet das Blech vor, so dass es mit absoluter Präzision zum Tiefziehen ankommt. Es achtet auf charakteristische Punkte, typischerweise auf Eckpunkte. Viktor Montag zählt derweil die Daten auf: Die Kopfpresse, in der die Umformung stattfindet, wiegt 2100 Tonnen, die Folgepressen 1200 Tonnen.
Am Ende des Prozesses sehen wir uns einige Bauteile an. Aber nicht allein, 7-8 Arbeiter entlang der beiden Linien (die meisten Bauteile werden paarweise hergestellt) führen eine schnelle Sichtprüfung durch, wobei die Zeit für die Entdeckung eines Fehlers im einstelligen Bereich in Sekunden liegt. Ein weiterer Kollege führt in einstündigen Zyklen (jede Stunde oder je 400 Teile) eine gründlichere Prüfung durch – mit einem Schleifstein wird die Oberfläche abgezogen, um Oberflächenfehler zu erkennen, Löcher werden gezählt – und andere Qualitätskriterien werden überprüft. Die Qualitätskontrolle erfolgt also auch während der TT-Fertigung – sozusagen – kontinuierlich. Es gibt außerdem eine von den Mitarbeitenden im Presswerk unabhängige Kontrolle durch die Qualitätssicherung – ein Bauteil pro Produktion wird herausgenommen und gründlich geprüft. Dies geschieht durch die Qualitätssicherungsabteilung hier im Presswerk. Liegt ein Fehler vor, müssen sofort die fehlerhaften Produkte gefunden, die Ursache des Fehlers ermittelt und behoben werden.
Federleichte Bauteile
Wir bewegen uns zwischen fertigen Produkten und Mustern: Wir sehen uns das Äußere und das Innere von Radhausschalen aus Stahl an, und dies hier ist eine Bodenplatte. „Der Stahl hat ein bisschen Orangenhaut, das ist bei diesem Bauteil kein Problem, aber bei dem sichtbaren Aluminiumkotflügel, da muss die Ausführung perfekt sein", weiht uns Viktor in die Geheimnisse ein. Das Bauteil ist federleicht, ich hebe es mit einem Finger an. Der Rahmen der Frontscheibe des Roadsters ist auch leicht, nur seine Herstellung ist es nicht. Die Hauptschwierigkeit besteht darin, dass viele Windschutzscheibenrahmen von einer einzigen Rolle kommen, wobei die Verarbeitung von Aluminium mit der Zeit immer schwieriger wird. Eine Rolle kann mehr als ein Jahr halten, und das Material muss speziell auf seine weitere Verwendbarkeit geprüft werden. Zum Vergleich: Bei einer Seitenwand wird jeweils eine Rolle geschnitten, und die Bleche bzw. Pressteile sind innerhalb weniger Wochen verbraucht. „Das ist also ein echtes Problem, wie wir das wirtschaftlich bewerkstelligen", sagt Viktor. Die Lösung ist: Mehr Roadster kaufen, Leute! – aber das wird bereits von mir beim Ausgang des Presswerks hinzugefügt, wo wir endlich wieder hören können – die Pressen sind nämlich ziemlich laut.
Kleine Stückzahlen und Aluminium – das ist typisch für den TT. Wir erfahren auch, dass das Material 2-3 Monate in der Rollenform, einen Tag im Rollenpuffer, eine Stunde auf der Schneidemaschine, ein paar Tage als Blech verbringt, um nach fünf Minuten als Bauteil die Presse zu verlassen. Am Ende des Prozesses sehe ich bekannte Formen. Wie wird die Seitenwand gefertigt? „Auf der Schneidemaschine schneiden wir die Dehnungslöcher und die Ecken aus, im Wesentlichen erhalten wir einen sehr breiten Umriss, dann gehen wir zum Tiefziehen über, wo nichts geschnitten wird. Dann, nachdem der Großteil der Form fertig ist, schneiden wir in Abschnitten und formen nach, schärfen den Radius der markanten Kanten, bereiten die Tanköffnung und die Radhäuser vor, und dann machen wir weitere kleine Schnitte, Formungen, Bohrungen und Löcher. All dies lässt sich nicht in einem Arbeitsgang durchführen, sondern muss getrennt geschehen, zumindest bei uns. Das ist eine Frage der Konstruktion und der Werkzeugbaukosten“, erklärt Viktor.
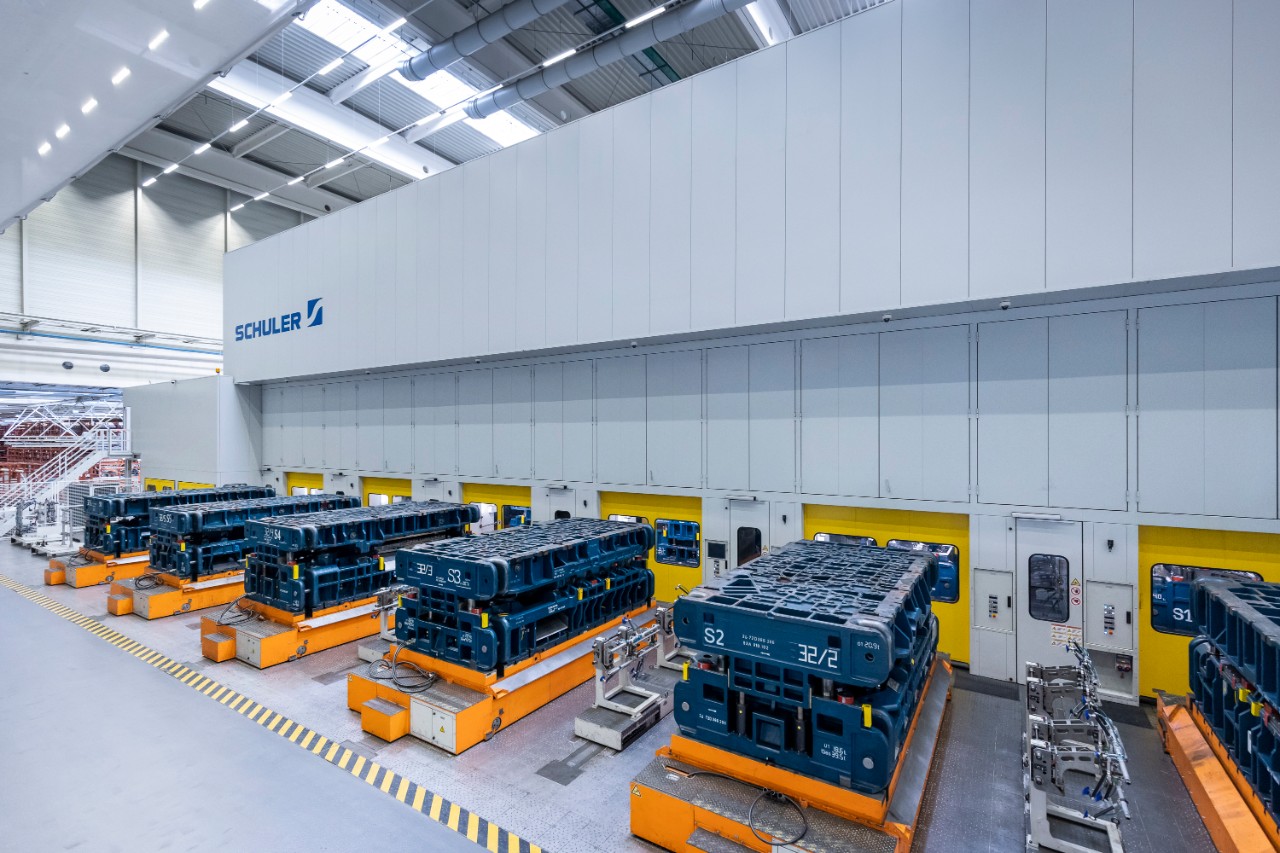
Aber natürlich kann der TT nicht rein rational, auf der Basis von Zahlen betrachtet werden; auch Emotionen spielen eine wichtige Rolle. Wie alle Mitarbeitenden bei Audi Hungaria bedauert auch Viktor den Abschied von diesem legendären Modell sehr. „Obwohl der TT aus fertigungstechnischer Sicht uns einige Schwierigkeiten bereitet, lieben wir ihn sehr, denn er gehört zu uns und seine dritte Generation ist durch und durch aus Győr. Wir fertigen ihn voller Stolz, bis zum allerletzten Stück“, sagt Viktor abschließend.
Im nächsten Teil unserer Serie besuchen wir den Karosseriebau.