Az elektromobilitás nem csak a termelésünket határozza meg, hanem egyre fontosabb szerepet játszik fejlesztési tevékenységünkben is. Műszaki fejlesztésünk az AUDI AG harmadik legnagyobb fejlesztési központja, és egyben a konstrukció, szimuláció, valamint az akusztikai és szilárdságtani vizsgálatok kompetenciacentruma. Munkatársaink egészen a fejlesztés előtti fázistól a szériafejlesztésen át a sorozatgyártás támogatásáig kísérik az elektromos hajtásokat. A terület az elektromos hajtások vizsgálatát és tesztelését többek között back to back (azaz B2B) mérőpadok és akusztikai járatópad segítségével végzi.
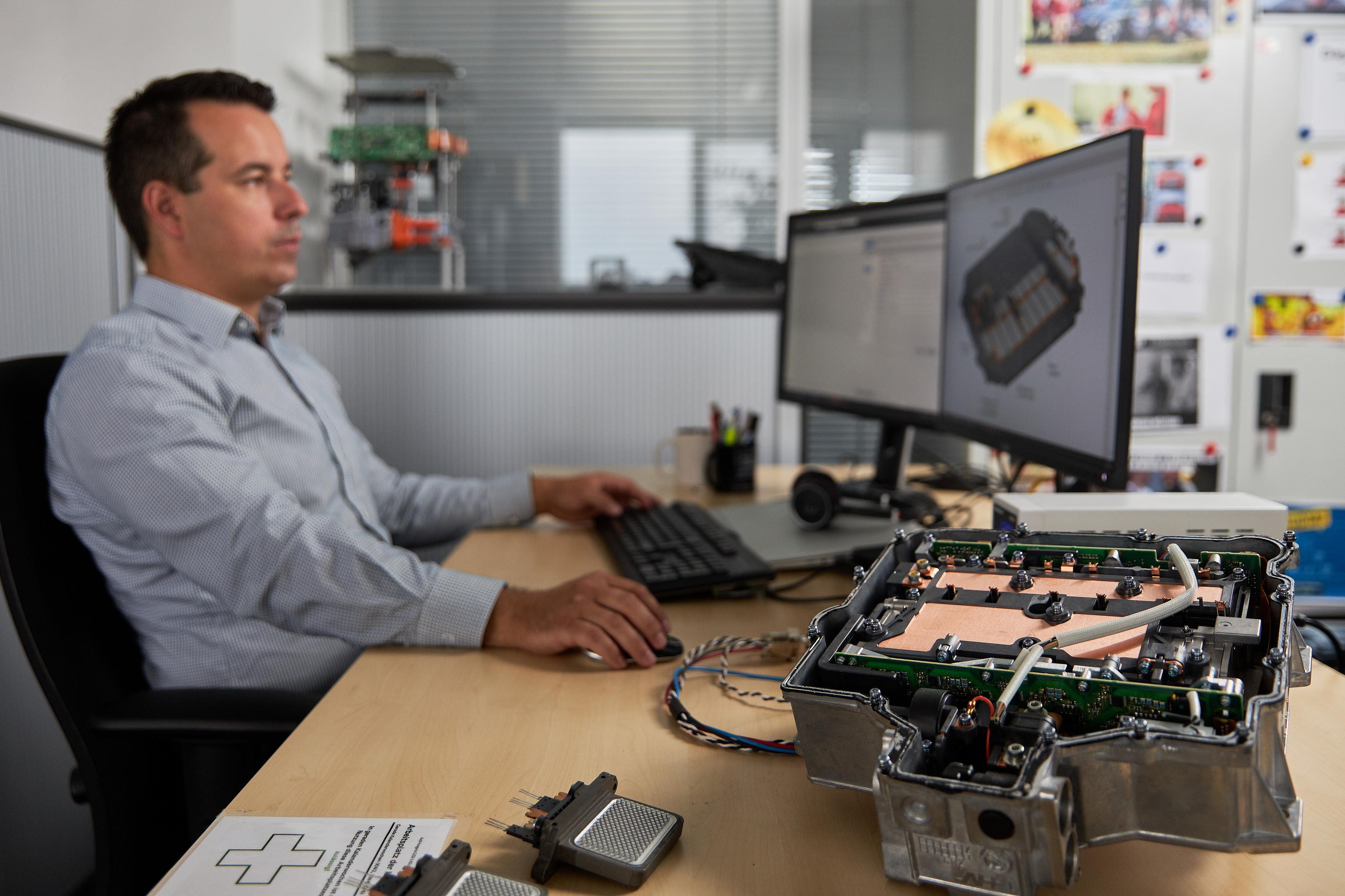
A villanymotor, a váltó és a teljesítményelektronika tökéletes együttműködése szükséges az elektromos hajtás hatékony és megbízható működéséhez. A Járműhajtás Fejlesztés specialistáinak egyik feladata éppen ezért az alkatrészek felelős tervezése, majd azok működésének tesztelése és engedélyezése. Tevékenységük kiterjed ezen felül az előszéria fázisában a villamoshajtások validálására, majd a szériagyártás támogatására is. Ennek biztosításához különböző próbapadokon végeznek részletes méréseket extrém termikus-, elektromos és mechanikai körülmények között.
A B2B próbapadokon használt felépítés két elektromos hajtásból, féltengelyekből és két homlokfogaskerekes hajtóműből áll. A tesztelés során az egyik villanymotor a hajtás funkciót veszi át, ezáltal a homlokfogaskereken keresztül hajtja meg a másik elektromos hajtást, így klasszikus értelemben ez utóbbi válik a tesztgéppé. A berendezés fő jellemzője, hogy fékgép nélkül működtethető, úgy, hogy két meghajtás egyidejű tesztelését lehetővé teszi. Ennek során az egyik elektromos hajtás motoros üzemben, a második pedig generátoros üzemben működik, váltokozó üzemmódban. Ez egyrészt lehetővé teszi a jóváhagyási folyamatok rendkívül hatékony és gyors elvégzését, másrészt a próbapad optimális felépítésének köszönhetően a homlokfogaskerék egyszerű átalakításával könnyen elérhető a nagyobb nyomaték vagy fordulatszám.
A B2B próbapad az időjárás próbáját is kiállja: a B2B vizsgálatok során alkalmazott paletták, amelyekre a villanymotort a munkatársak előre felépítik és a vizsgáló kamrába juttatják, működtethetők klímakamrában is. A klímakamra lehetővé teszi a hajtások tesztelését extrém időjárási viszonyok között, egészen a sarkvidéki hidegtől a szaharai forróságig, sőt még azon túl is: a szakemberek -70 ° C és 160 °C közötti hőmérséklettartományban tudják itt tesztelni a meghajtásokat, amelynek segítségével különböző, egészen extrém vezetési környezet is modellezhető, amelyekben később a hajtást ügyfeleink napi szinten használják. A külső hőmérséklet mellett az elektromos hajtás hűtőfolyadékának hőmérséklete is függetlenül beállítható -40 °C és 80 °C közötti tartományban. A tesztprofilok széles választéka futtatható a B2B tesztpad és a klímakamra kombinációjával, amely magában foglalja például a különböző éghajlati viszonyok között végzett élettartam-vizsgálatokat, valamint a hőmérsékleti határértékeken végzett kísérleteket is.
Az Audi a következő két évben kétszámjegyű eurómilliós összeget, több milliárd forintot fordít az Audi Hungaria Műszaki Fejlesztés területére. A beruházás középpontjában az elektromobilitás és a digitalizáció további fejlesztése áll, például a nagyteljesítményű elektromos motorok és hajtások számára a legmodernebb vizsgálóberendezések üzembe helyezésével.
Csatlakozz hozzánk és fejleszd velünk a jövő hajtásait Győrből: www.audi.hu/emotor
2018 óta már elektromos erőforrásokat is gyártunk Győrben az Audi e-tronok számára, a motorgyártás terén szerzett évtizedes tudást kiegészítendő azonban új kompetenciákra és új technológiára is szükség volt az elektromos hajtások gyártásához.
A tisztán elektromos Audi modellek felépítésében fontos szerepet játszik az elektromos modellek számára készülő erőforrások gyártásának csúcstechnológiájú berendezése, a réztekercselő. A gép a gyártási folyamat egyik legelső és legfontosabb pontján az elektromotor állórészéhez, a státorhoz szükséges réz tekercselését végzi. Ez egy automata behúzó, amely minden státorba réztekercset épít be. A teljes, 7,5 órás gyártási folyamat három fázisból áll. Miután a státor első fázisát behúzza a réztekercselő gép, és a kivezetései megkapják a szigetelőcsöveket, a státor egy formázóprésbe kerül, mely megformázza és kihajtja a lemezcsomagba behúzott rézdrótszálakat, hogy a következő fázis problémamentesen, géptörés nélkül legyen behúzható. A második fázisban megismétlődnek az előző folyamatok, a harmadikban befejeződik a tekercselés. Az új technológiák használatához munkatársaink sikerrel teljesítették egy alaposan megtervezett képzési stratégia követelményeit, megszerezve a szükséges szaktudást az e-motorok gyártásához. Ennek eredményeképpen 2018 óta már több mint 300 000 elektromos motort gyártottunk. Ennek a motorgeneráció gyártásának feltétele a nagy szaktudás és a precíz munka, amivel dolgozóink mindegyike rendelkezik.
Az Audi Hungariánál a jövő e-motorjai számára új gyártóterület lett kialakítva, ahová a vállalat számos, a sorozatgyártáshoz szükséges gyártóberendezést és eszközt telepített. Győrben készülnek majd azok az elektromos meghajtások, amelyek a Porschéval közösen kifejlesztett prémium elektromos platformra (Premium Platform Electric – PPE) épülnek. A státor- és váltókomponens- gyártás, valamint a meghajtások összeszerelése 15 000 m2-en indul. A jövőbeni három műszakos gyártási modellben közel 700 munkatárs munkahelyét biztosítjuk. De miben is hoz újdonságot a gyártásban a PPE? A fogaskereket teljesen újszerű, háromlépcsős folyamatban fogják gyártani. A folyamat az egyszerűbb fogazatok kialakításával és előmarásával kezdődik, ezt követően az összes darab hőkezelése a kopásállóság miatt, majd készre köszörülése, illetve a fogazatok hónolása.
Az új gyártóterület megtervezésének egyik különlegessége volt, hogy az Audi Hungariánál először használtak VR-szemüveget egy gyártósor tervezéséhez. Az újfajta 3D-képfeldolgozási technológiáknak köszönhetően a mérnökök képesek még jobban megtervezni és felépíteni a gyártási folyamatot, ezáltal egy hatékonyabban működő gyártóterület és ergonomikusabb munkahelyek alakíthatók ki. Ám nem ez az egyetlen nóvum a hagyományos robbanómotorok gyártásához képest. Különbség az is, hogy míg a belső égésű motoroknál a komplett váltót az autógyárak építik be, az elektromos meghajtások esetében azt összeépítik az erőforrással. Így az Audi Hungaria szakemberei előbb elkészítik a komponenseket, amelyeket aztán a szereldébe szállítva összeépítenek az e-motorral.
Tervezd velünk te is a következő generáció gyártósorait az Audi Hungariánál és légy részese csapatunknak, akik a világ legnagyobb motorgyárának gyártósorait keltik életre! Tudj meg többet itt: www.audi.hu/gyartastervezes